平衡机用于检测和修正旋转机械部件(如转子、风扇、涡轮等)的不平衡状态。在进行旋转设备的振动信号分析时,通常会遵循以下步骤:
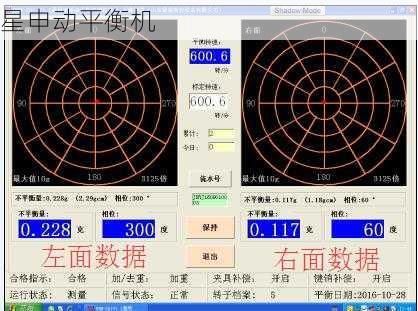
1. 安装传感器:
在待测旋转部件上安装振动传感器(通常是加速度计或位移传感器)。传感器应安装在对振动最敏感的位置,以确保能够捕捉到尽可能多的信息。
2. 数据采集:
启动旋转设备,并使用数据采集系统记录来自传感器的振动信号。这通常需要设定合适的采样频率,以保证能准确捕获振动特征而不发生混叠现象。
3. 预处理数据:
对采集的数据进行必要的预处理,比如滤波去除噪声、基线校正等,以提高后续分析的准确性。
4. 频谱分析:
利用快速傅里叶变换(FFT)将时域信号转换为频域信号,从而可以识别出不同频率成分对应的幅值大小。对于旋转设备而言,重点关注与旋转频率及其谐波相关的峰值。
5. 特征提取:
从频谱中提取关键特征参数,例如特定频率下的振幅、相位角等信息。这些特征可用于判断是否存在不平衡问题以及其严重程度。
6. 诊断不平衡:
分析所提取的特征来确定是否存在不平衡情况。一般来说,如果某个频率(通常是旋转频率的一阶或高阶谐波)显示出异常高的振幅,则可能是由于该处存在不平衡所致。
7. 定位不平衡位置:
通过相位分析或者使用多个传感器测量不同方位上的振动差异,可以更精确地定位不平衡发生在哪个方向或区域。
8. 调整与验证:
根据上述分析结果,在适当的位置添加或移除质量块来进行平衡调整。然后重新运行设备并重复以上过程直至振动水平达到可接受范围之内。
9. 报告生成:
完成所有测试后,整理相关数据形成报告,包括原始振动状态、采取措施后的改善效果等内容。
现代平衡机往往配备有自动化软件工具,它们可以帮助工程师更加高效地完成上述任务,并提供直观的图形界面显示分析结果。此外,随着技术进步,一些高级功能如机器学习算法也被应用于振动信号分析当中,使得故障预测变得更加智能和精准。