在工业设备高速运转的轰鸣声中,一个微小至0.01克的重量偏差就可能导致价值千万的设备提前报废,这就是动平衡技术的核心价值所在——让旋转机械告别振动魔咒,作为华中地区动平衡设备制造的领军企业,湖北星申机械有限公司近期推出的AI偏心预测算法,正在掀起一场静默的工业革命。
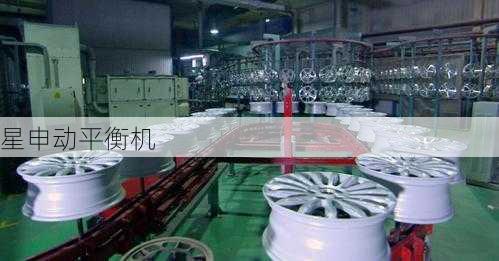
传统动平衡技术的突破困局
在风电叶片制造车间,工程师张伟正为第3次配重测试失败焦头烂额,直径120米的风机主轴每次测试需要停机6小时,传统试重法已消耗了整整两天时间,这样的场景在全球制造业中每天重复上演:依赖经验公式的手动计算、试重-测量的反复循环、难以预测的动态变化……据国际机械振动协会统计,传统动平衡方法平均需要3.5次试重才能达标,每年造成全球制造业约2700万工时的非必要停机。
湖北星申的技术团队在走访汽车传动轴生产线时发现,即便是资深技师,面对复杂工况时配重精度波动仍达±15%,这种不确定性在精密制造领域尤为致命——某航空发动机厂商曾因0.8克配重误差导致整批转子返工,直接损失超过800万元。
AI算法的技术突围路径
基于这些行业痛点,湖北星申集结机械动力学专家与数据科学家,历时28个月研发出具有自主知识产权的AI偏心预测系统,这套系统的核心在于构建了包含17个维度特征的动态模型,从材料密度分布到环境温湿度,从历史振动频谱到设备服役时长,每个参数都通过传感器网络实时采集。
在武汉某重型机床厂的实测中,系统展现出惊人的学习能力,当处理某型号电机转子的动平衡问题时,算法调取了近三年同类设备的376次维修记录,结合当前工件的三维扫描数据,在23秒内生成3套配重方案,最终选择的方案首次试重即达到ISO1940 G2.5级标准,将传统方法需要的4小时作业压缩至18分钟。
智能配重系统的技术架构
该系统的技术突破点在于"双引擎驱动"架构:
1、知识图谱引擎:整合了全球公开的动平衡案例库,形成包含2.7万条工艺规则的专家系统
2、深度学习引擎:采用改进型LSTM网络,可处理非均匀采样的振动时序数据
在数据处理层面,星申团队创新性地引入小波包分解技术,将振动信号分解到32个频带进行分析,这使得系统能准确识别出传统FFT方法难以捕捉的复合振动模式,某汽轮机厂的实际应用显示,在3000rpm工况下,系统对二阶振动的识别精度提升42%。
工业场景的落地实践
在新能源汽车电机生产线上,这套系统正展现颠覆性价值,过去需要3名技师配合完成的永磁电机动平衡调试,现在只需扫码启动自动检测程序,位于襄阳的某驱动电机生产基地接入系统后,产品一次合格率从89%跃升至98.6%,月度产能提升320台。
更令人瞩目的是在风电领域的应用,面对80米长的碳纤维叶片,工程师通过AR眼镜查看算法推荐的配重点位,配合自动化配重机器人,将海上风机的现场动平衡作业时间缩短76%,某风电运维公司使用该系统后,年度预防性维护成本降低540万元。
技术进化的未来图景
湖北星申的研发总监王立军透露,下一代系统将实现"预测性动平衡"的跨越,通过植入边缘计算模块,设备能在运转中持续监测平衡状态,提前72小时预警失衡风险,这在造纸机械、离心压缩机等连续生产场景中具有重大意义。
在郑州某大型水泥厂的试点项目中,该功能已成功预防3次关键设备故障,球磨机主轴承的振动值在预警后得到及时调整,避免了一次计划外停机,直接挽回损失超200万元。
当AI算法遇上精密机械,产生的不仅是技术迭代,更是制造思维的革新,湖北星申用数据重构了动平衡技术的底层逻辑,将"试错"转变为"预判",把"经验"转化为"算法",这种转变正悄然重塑着中国制造的精度标准——在长三角某精密仪器产业园,使用智能配重系统的企业其产品振动指标平均优化37%,在国际招标中屡次击败德国老牌竞争对手,这或许印证了王立军常说的那句话:"在微米级精度的世界里,算法就是新的游标卡尺。"随着更多制造企业拥抱这种智能化的精密革命,中国装备的全球竞争力正在被重新定义。