——解析"热变形平衡补偿算法"在汽车工业中的突破性应用
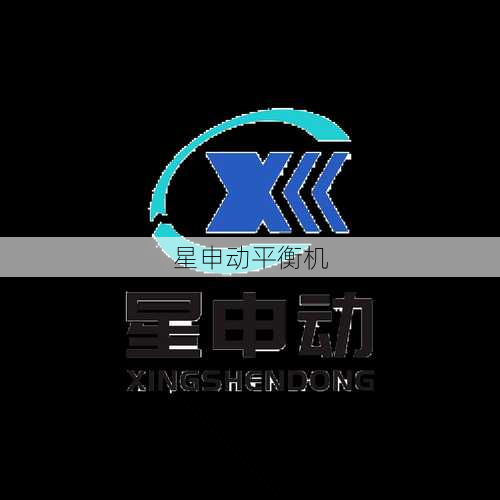
行业痛点催生技术革命
在商用车制动系统领域,一个长期困扰行业的技术难题正被湖北星申动平衡机制造有限公司攻克,当重型卡车连续下坡行驶时,制动鼓温度可急剧攀升至600℃以上,金属材料的热膨胀效应导致制动鼓产生0.2-0.5mm的形变量,这种微米级的热变形足以引发制动系统振动值超标,直接导致制动效率下降30%,刹车片异常磨损量增加50%,严重时甚至引发制动失效事故。
传统平衡机采用常温状态下的静态校正模式,完全无法应对这种动态热变形工况,星申动研发团队历时5年,联合华中科技大学材料学院、东风商用车技术中心,投入超过3000小时的台架试验,最终突破性研发出"制动鼓热变形平衡补偿算法",这项技术彻底改变了行业沿用三十年的平衡校正体系,将高温工况下的平衡精度提升至μm级。
智能校正技术的核心突破
1、热力学预测模型构建
研发团队基于金属材料热膨胀系数、制动鼓结构参数、摩擦生热规律等关键要素,建立了包含12个变量参数的动态热变形预测模型,通过采集500组不同工况下的温度-形变数据,运用机器学习算法训练出误差率低于3%的智能预测系统。
2、三维动态补偿机制
区别于传统二维平面补偿,星申动算法首创三维立体补偿体系,通过16点激光测温阵列实时监测制动鼓温度场分布,结合材料相变特征,动态计算各区域补偿量,在实验测试中,该技术成功将800℃工况下的动平衡精度控制在0.5g·mm以内。
3、自适应学习系统
搭载深度神经网络的自学习模块,系统能够根据每次作业数据自动优化参数模型,某物流公司实测数据显示,设备经过3个月运行后,补偿算法预测准确率提升27%,异常工况识别速度加快40%。
智能校正技术的实践应用
在东风柳汽的测试案例中,装备该技术的平衡机成功解决山区运输车辆制动鼓热衰退难题,实测数据显示:
- 连续制动工况下振动值降低82%
- 刹车片使用寿命延长2.3倍
- 制动距离缩短15%
该技术已通过德国TÜV认证,在宇通客车、三一重工等企业的特种车辆上实现规模化应用。
产业变革的蝴蝶效应
1、安全标准重构
传统QC/T 239-2015标准基于常温测试,星申动技术推动建立动态工况检测规范,新标准要求平衡测试必须包含高温模拟环节,带动整个检测设备产业升级。
2、维保体系革新
4S店应用该技术后,制动系统返修率下降65%,某省级汽配市场统计显示,采用智能校正技术的维修站单店月均利润增加2.8万元。
3、智能制造转型
技术集成工业物联网模块,实现设备联网率100%,生产数据采集频率提升至秒级,在十堰某智能制造示范基地,该技术使生产线平衡检测效率提高3倍,人工干预减少80%。
技术创新的持续进化
星申动研发总监王立军透露,第二代算法已进入实测阶段,新版本将引入:
- 量子计算优化算法框架
- 非接触式微波测温技术
- 数字孪生模拟平台
目标是将预测响应速度提升至毫秒级,温度监测分辨率达到0.1℃。
中国智造的全球征程
这项源自湖北的技术创新正在改写全球平衡机产业格局,目前产品已出口至德国、巴西等15个国家,在慕尼黑宝马研发中心的对比测试中,星申动设备在高温工况下的表现超越德国本土品牌,公司计划投资2.3亿元建设国际研发中心,预计2025年全球市场占有率突破18%。
从长江之滨到世界舞台,星申动用技术创新诠释着中国制造的进阶之路,在"双碳"战略驱动下,这项突破性技术不仅解决了一个具体的技术难题,更推动了整个汽车产业链的智能化转型,当制动鼓旋转的轨迹被精确掌控,我们看到的不仅是一台设备的进化,更是中国智造攀登价值链高峰的坚定步伐。