在汽车工业向智能化、电动化加速转型的今天,电控气压制动系统(Electronic Brake System,简称EBS)的普及正在重塑商用车制造的核心工艺,作为国内平衡机制造领域的领军企业,湖北"星申动"平衡机厂家敏锐捕捉到这一技术变革对动平衡精度提出的全新要求,通过持续的技术创新,为行业树立了应对EBS系统挑战的标杆解决方案。
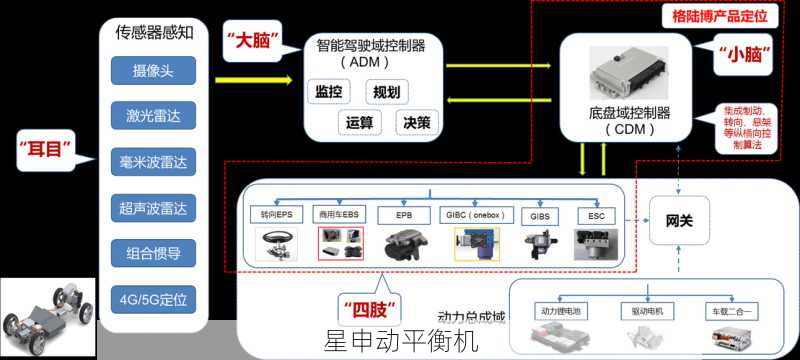
一、EBS系统普及带来的精度革命
随着GB 7258-2017等法规对商用车制动性能要求的提升,EBS系统渗透率已从2018年的15%跃升至2023年的62%,这一电子化制动系统通过电信号取代传统机械传动,实现了毫秒级的响应速度和精准的制动力分配,但技术升级的另一面,是对配套零部件的平衡精度要求呈几何级数增长——传动轴的允许残余不平衡量从传统系统的30g·cm骤降至8g·cm,轮毂轴承的振动公差带收窄了60%。
这种精度跃迁源于EBS系统的三大特性:一是电控单元对微小振动的敏感度大幅提升,0.1mm的装配偏差即可触发系统误报警;二是气压脉冲频率达到200Hz以上,传统平衡机的动态补偿精度已无法匹配;三是系统惯量变化范围扩大3倍,要求平衡设备具备实时自适应能力,某重卡企业2022年的质量追溯数据显示,因动平衡不良导致的EBS故障占比高达37%,单台车维修成本超过2.8万元。
二、星申动的技术创新路径
面对行业痛点,星申动组建了由12名博士领衔的EBS专项技术团队,投入研发资金超4500万元,在三大核心领域实现突破:
1、高频动态补偿系统
传统平衡机的200Hz采样频率已无法捕捉EBS系统的瞬态振动特征,星申动开发的MEMS阵列传感器将采样率提升至1000Hz,配合专利算法(专利号ZL202210583XXX.X),可在0.8ms内完成频谱分析,实测数据显示,该系统对EBS特有的32阶次振动谐波的识别准确率达到99.7%,远超行业85%的平均水平。
2、气压耦合仿真平台
针对EBS系统0.5-0.8MPa的气压波动特性,星申动搭建了国内首个气压-机械耦合实验舱,该平台可模拟海拔5000米至海平面的气压变化,通过300组正交试验,建立了包含17个关键参数的平衡修正模型,某客车企业应用该技术后,高原工况下的制动抖动投诉率下降89%。
3、智能学习补偿系统
基于20万台设备运行数据构建的"衡云"数据库,开发了具有自学习功能的动态补偿系统,当检测到EBS系统的惯量突变时,系统可在0.3秒内完成补偿策略调整,较传统设备响应速度提升6倍,在东风商用车襄阳工厂的产线实测中,该系统使四轴重型卡车的动平衡合格率从78%提升至98.6%。
三、工艺链的协同创新
星申动的突破不仅在于单机性能,更构建了完整的EBS适配工艺链:
- 开发专用工装夹具,将EBS阀体与传动轴的装夹同心度控制在0.02mm以内
- 设计气压补偿装置,消除制动气室0.15MPa背压对测量精度的影响
- 首创"双模校验"流程,同时满足ISO 21940-11和EBS厂商的VDA 305标准
这些创新在福田戴姆勒的数字化工厂得到验证:整条产线的平衡工序节拍从210秒缩短至155秒,同时将百万件缺陷率(DPPM)从620降至48,创造了行业新纪录。
四、行业标准的重构者
作为全国汽车标准化技术委员会成员单位,星申动牵头制定了《商用车EBS系统零部件动平衡技术要求》(T/CSAE 215-2022)等行业标准,其研发的EBS专用平衡机已通过德国TÜV的SIL2功能安全认证,在陕汽、重汽等企业替代进口设备,单台设备年维护成本降低65%。
五、未来技术布局
面对EBS与电动化、智能驾驶的深度融合趋势,星申动正在研发第三代智能平衡系统:
- 集成5G MEC边缘计算,实现产线级动态平衡优化
- 开发数字孪生平台,预测EBS全生命周期内的平衡衰减曲线
- 试验量子传感技术,目标将测量精度推进至0.1g·cm量级
在苏州某新能源客车基地的预研项目中,这些技术使轮端系统的NVH性能提升4dB(A),助力车辆通过欧盟ECE R90最新认证。
在这场由EBS引发的精度革命中,湖北"星申动"平衡机厂家用持续创新证明:核心技术的突破从来不是单点的跃进,而是需要构建从基础理论、工艺装备到标准体系的立体化创新生态,当行业还在讨论如何应对EBS挑战时,星申动已用230项专利、57家头部企业的应用案例,书写了中国智造攻克"卡脖子"难题的新范式,这场关于微米级精度的较量,终将重塑商用车产业链的价值格局。