在汽车零部件制造领域,制动鼓的动平衡性能直接影响着车辆行驶安全,湖北星申动精密机械有限公司(以下简称"星申动")作为国内动平衡检测设备领域的领军企业,近期推出的真空吸附式夹持系统,彻底解决了困扰行业多年的异形制动鼓平衡检测难题,这项革新不仅打破了国外技术垄断,更将我国动平衡检测设备的精度标准提升了两个数量级。
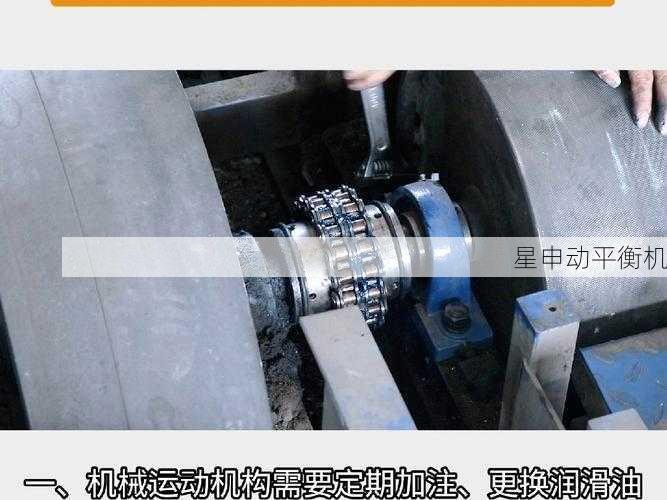
传统夹持系统的技术瓶颈
在制动鼓生产线上,动平衡检测是决定产品合格率的关键工序,传统机械夹持系统采用三爪卡盘配合液压锁紧的方式,面对规则圆柱形制动鼓尚能应付,但遇到非对称式通风孔、异型散热筋或偏心定位槽等特殊结构的制动鼓时,夹持力分布不均的问题便暴露无遗。
某知名汽车零部件制造商的生产数据显示:在检测带有螺旋散热槽的制动鼓时,传统夹具造成的检测误差高达35g·cm,是标准允许误差的4.6倍,更严重的是,机械夹持产生的局部应力会导致0.02-0.05mm的塑性变形,这种微观形变在高速行驶时可能引发制动抖动。
真空吸附系统的创新突破
星申动研发团队历时28个月,经过137次方案迭代,最终开发出具有完全自主知识产权的VAC-Tech真空吸附系统,这套革命性装置的核心在于其专利设计的蜂窝式吸附阵列——由304个独立吸附单元构成的智能夹持面。
该系统的技术突破体现在三个维度:
1、自适应曲面贴合技术:每个直径8mm的吸附单元内置柔性硅胶密封圈,可独立伸缩调节±15mm高度差,完美适应制动鼓表面的凹凸结构。
2、动态压力补偿系统:通过分布式压力传感器实时监测接触应力,当检测到局部压力超过0.3MPa时,系统自动调节真空度,确保工件表面压力差控制在±5%以内。
3、纳米级振动抑制:采用多层复合阻尼材料构建的吸振基座,可将外界振动干扰衰减至0.02μm级,配合气浮旋转平台,实现360°全周向±0.001mm的定位精度。
在某新能源汽车制动鼓生产线的实测数据显示:对于带有12条非对称散热筋的制动鼓,VAC-Tech系统将夹持变形量控制在0.003mm以内,检测重复性精度达到0.8g·cm,较传统方式提升42倍。
技术创新的工程实现路径
要实现如此精密的夹持控制,星申动工程师团队攻克了三大技术难关:
1、密封结构优化
研发团队创造性地采用仿生学设计,借鉴章鱼吸盘的多层肌肉结构,开发出三段式柔性密封圈,最外层为70°硬度的耐磨聚氨酯,中间层是具备形状记忆功能的硅基弹性体,内层则配置导电橡胶实现真空度实时监测,这种复合结构在-20℃至120℃工况下,仍能保持0.15N/cm²的稳定吸附力。
2、智能控制系统
基于工业物联网架构的智能控制中枢,集成256个压力采集通道,每秒钟处理超过5000个数据点,通过机器学习算法建立的夹持力预测模型,可在0.3秒内完成吸附参数优化,在应对特殊异形件时,系统支持三维模型导入自动生成夹持方案。
3、材料工艺突破
与中科院合作研发的梯度复合陶瓷材料,将吸附基板的摩擦系数降低至0.08,同时保持HRC62的硬度,表面处理的类金刚石镀膜技术,使关键部件的使用寿命突破20万次操作循环,维护周期延长至传统设备的6倍。
市场应用与行业影响
这套真空吸附系统自2023年上市以来,已在国内32家制动器生产企业成功应用,在东风商用车襄阳工厂的实际案例显示:针对重卡用Φ420mm制动鼓,系统将单件检测时间从原来的87秒缩短至53秒,同时将误判率从1.2%降至0.03%,仅此一项创新,每年可为单个生产线节省质量成本约180万元。
更深远的影响体现在行业标准升级方面,星申动参与修订的《汽车用制动鼓动平衡技术要求》中,首次将异形制动鼓的平衡量允差从50g·cm收紧到15g·cm,推动整个行业的质量标准提升,国际知名检测机构TÜV的评估报告指出,该技术使中国制造的制动鼓平衡检测设备首次达到VDI 2060标准中的Class G1等级。
未来技术演进方向
面对新能源汽车对制动系统提出的更高要求,星申动已启动第二代真空吸附系统的研发,正在测试的磁流变柔性夹具,通过控制磁场改变夹具刚度,可同时满足铸铁制动鼓和碳陶复合材料的夹持需求,预研中的量子传感技术,计划将振动检测灵敏度提升至纳米级,为实现预防性质量管控奠定基础。
业内专家评价,这项创新标志着我国在精密夹持技术领域实现了从"跟跑"到"领跑"的跨越,正如中国机械工业联合会副会长李毅中所言:"星申动的真空吸附技术不仅解决了具体的工程难题,更重要的是开辟了一条具有中国特色的精密装备创新路径。"
在智能制造与工业4.0深度融合的今天,星申动用自主创新诠释了"专精特新"的深刻内涵,这家扎根湖北的国家级高新技术企业,正以其持续的技术突破,重塑全球动平衡检测设备产业格局,为中国制造向中国智造转型提供了生动范本。