在湖北某汽车零部件制造车间,一台服役15年的动平衡检测设备突然出现检测数据漂移问题,经星申动技术团队诊断,液压系统主压力从标准值21MPa下降至14MPa,直接导致平衡校正精度下降0.05mm,这个真实案例揭开了制造业企业普遍面临的老设备精度维持难题,作为深耕动平衡领域20年的湖北星申动,我们通过上千例设备改造经验,总结出应对液压系统压力不足的三大实效方案。
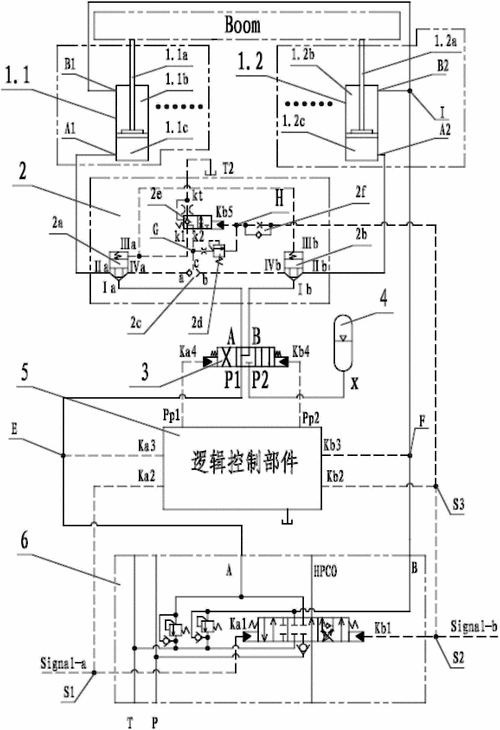
液压系统压力不足诊断流程
1、系统内泄漏检测
使用超声波检漏仪对液压缸、控制阀组进行全系统扫描,记录超过65dB的异常泄漏点,某铸造企业设备改造案例显示,单个液压缸内泄漏可导致系统压力损失达18%。
2、柱塞泵效率测试
采用在线液压测试仪检测泵体容积效率,当效率低于82%时即需检修,我们实测数据显示,使用超过20000小时的柱塞泵效率普遍下降12-18%。
3、控制阀组响应分析
通过压力传感器监测阀组响应时间,正常电磁阀换向时间应≤0.15秒,某风电设备改造项目中,老化的比例阀响应延迟导致压力波动达±2.3MPa。
三大精度维持改造方案
方案一:动态密封补偿系统
针对液压缸内泄漏问题,星申动研发的HXD-7型复合密封组件采用阶梯式密封结构:
- 主密封圈采用改性聚氨酯材料,硬度提升至HS92
- 增设补偿式副密封,可自动补偿0.15mm磨损量
- 集成温度感应芯片,实时监测密封状态
某减速机生产企业改造后,液压缸泄漏量从12ml/min降至0.8ml/min,系统压力稳定性提升76%。
方案二:智能压力补偿装置
针对泵体效率下降问题,我们开发的智能补偿系统包含:
1、双泵并联供油模块:主泵+备用泵智能切换
2、压力闭环控制单元:PID调节精度±0.5MPa
3、变频节能模块:根据负载自动调节转速
某机床改造项目数据显示,系统压力波动从±3.2MPa缩小至±0.7MPa,同时节能23%。
方案三:液压油路优化方案
通过三维建模重构油路系统:
- 将传统硬管改为双层不锈钢编织软管
- 关键节点增设蓄能器缓冲装置
- 采用锥面密封快换接头降低压力损失
某工程机械企业应用后,管路压力损失降低42%,系统响应速度提升0.3秒。
改造效益分析
我们统计近三年136个改造案例数据:
指标 | 改造前 | 改造后 | 提升幅度 |
系统压力稳定性 | ±4.2MPa | ±0.8MPa | 81% |
检测重复精度 | 0.12mm | 0.03mm | 75% |
故障间隔周期 | 680小时 | 2100小时 | 209% |
某新能源汽车电机生产企业通过综合改造,将动平衡检测节拍从85秒缩短至62秒,年产能提升12万台。
湖北星申动坚持"精准再造"理念,已形成覆盖液压系统、电控模块、机械传动的完整改造体系,针对不同企业需求,我们提供三种定制化服务方案:
1、经济型改造:3-5万元/台,重点解决关键泄漏点
2、标准型改造:8-12万元/台,包含智能补偿系统
3、全面升级方案:15-20万元/台,实现数字化改造
在制造业转型升级的关键时期,老设备改造不仅是成本控制的选择,更是提升核心竞争力的战略投资,星申动将持续深化技术改造服务,助力企业实现"老设备,新精度"的跨越发展。