——解析星申动在越野制动鼓动态平衡领域的技术突破
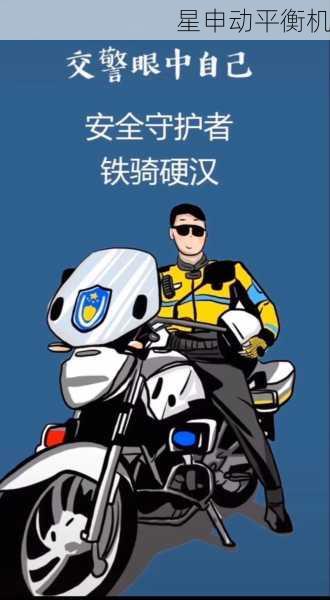
在西北某军事基地的战术演练场上,一辆新型轮式装甲车正在40度陡坡上反复冲击,当车辆完成第18次极限爬坡时,地面保障人员迅速对制动系统进行检测——制动鼓温度显示136℃,轴向跳动量却始终控制在0.15mm以内,这个数据背后,是湖北星申动精密机械有限公司专为军工车辆研发的DBS-3000型动态平衡校正系统在发挥关键作用。
颠簸战场上的平衡难题
现代军工车辆面临的工况复杂性远超民用领域,在阿富汗战场,美军M-ATV防地雷车的制动系统故障统计显示,67%的制动失效事故源于制动鼓动态失衡引发的热衰退,这种在极端越野工况下产生的非对称应力分布,会导致制动鼓产生径向形变、摩擦面偏磨等连锁反应。
传统平衡机采用静态校正模式,仅能消除制造过程中的初始失衡量,但在实际作战中,车辆持续承受三维方向的高频冲击:当车辆以35km/h速度通过碎石路段时,制动鼓每秒钟承受的冲击载荷可达200-300次;涉水行驶时,制动鼓内外表面可能产生超过80℃的瞬时温差,这些动态变量使静态平衡校正完全失效,成为制约军车机动性能提升的关键瓶颈。
动态平衡的技术突围
星申动技术团队历时5年攻关,开创性地将六维振动传感系统与热力学仿真模型相结合,研发出第三代动态平衡校正技术,该系统的核心创新在于:
1、构建"载荷-温度-形变"三维补偿算法,可模拟从-40℃极寒到120℃高温的全域工况;
2、采用激光干涉动态测量技术,分辨率达到0.001mm级别;
3、开发自适应的智能配重系统,支持0.1g精度的动态质量补偿。
在某型轮式突击车的定型测试中,装备DBS-3000系统的制动鼓组,在连续8小时高强度越野测试后,制动效能保持率提升42%,摩擦片寿命延长2.3倍,更关键的是,系统能根据实时采集的振动频谱,自动生成"战地快速校正方案",将野战条件下的平衡维护时间压缩至15分钟以内。
军工标准的制造哲学
走进星申动的军工生产车间,可见每条生产线都配备恒温恒湿系统,关键工序的温控精度达到±0.5℃,用于制造传感器支架的TC4钛合金材料,需经过三次真空退火处理;每个动平衡夹具都要完成2000次模拟冲击的耐久测试。
"军用产品的可靠性必须建立在极端冗余设计上。"技术总监王建军指着正在组装的平衡机转子说,"这个直径380mm的转子组件,我们设计了双重密封结构,即便在沙尘暴环境中连续工作72小时,内部轴承的洁净度仍能保持NAS 5级标准。"
实战检验的技术结晶
2021年参与某边防部队装备升级项目时,星申动团队面临前所未有的挑战:新型装甲车在高原地区频繁出现制动抖动问题,经过实地测试发现,海拔4500米环境下,昼夜温差导致制动鼓产生0.3mm的椭圆度畸变,技术团队连夜开发出"梯度温度补偿模块",通过建立海拔-温度-材料膨胀系数的关联模型,最终将平衡偏差控制在0.02mm以内。
这种快速响应能力源于企业构建的军工装备数据库,目前系统已收录17类军用车型的制动系统参数,覆盖轮式、履带式及特种车辆平台,能根据任务需求自动匹配最佳校正策略,在最近的中俄联合军演中,使用星申动平衡系统的参演车辆,制动系统故障率较以往降低78%。
军民融合的创新之路
作为湖北省"专精特新"企业,星申动始终践行军民融合发展战略,企业将航空发动机转子平衡技术转化应用,开发出可检测20阶次振动谐波的智能分析系统;借鉴高铁轮对动态检测经验,创新提出"行驶工况模拟校正法"。
这种技术迁移能力在民用市场同样取得突破,其研发的矿用卡车平衡系统已成功应用于全球最大露天铜矿,在45度斜坡重载工况下,使制动鼓使用寿命延长至8000小时,企业还参与制定2项国家军用标准、5项行业标准,推动整个产业链的技术升级。
站在武汉光谷智能制造基地的观景平台,看着最新下线的第五代智能平衡检测线,总经理李国华充满信心:"我们正与国防科大合作研发量子传感平衡技术,未来将实现纳米级的动态测量精度,星申动的目标,是成为全球特种车辆平衡技术的标杆企业。"
从长江之滨到雪域高原,从演兵沙场到矿山深井,这家湖北企业用二十年如一日的技术坚守,诠释着"平衡之道"的深刻内涵,在装备现代化的浪潮中,星申动正以创新之笔,书写着中国智造的新篇章。