在鄂西北某水稻种植基地,一台联合收割机因制动系统异常被迫停工,经检查发现,制动鼓表面附着3mm厚的泥浆结块,平衡参数偏差超过ISO标准值3倍有余,这个场景折射出我国农用机械领域长期存在的技术痛点——泥水腐蚀对制动系统造成的平衡性破坏,作为深耕动平衡领域17年的专业厂商,湖北星申动平衡机制造有限公司凭借独创的"三阶九步"预处理方案,为这一行业难题提供了创新解决方案。
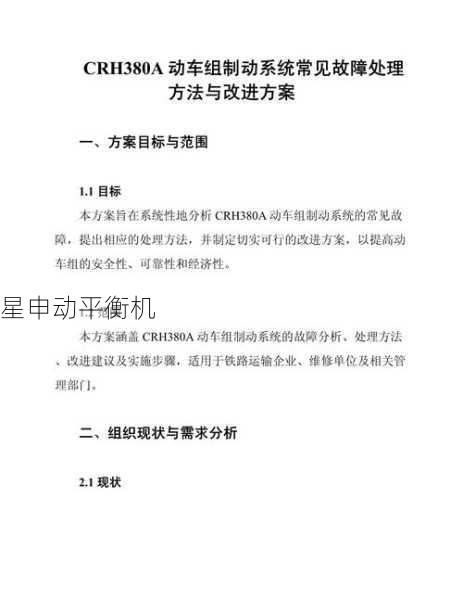
泥水腐蚀对农机制动系统的双重破坏
在田间作业环境中,农机设备需要长期接触pH值4.5-8.5的泥水混合物,这种特殊工况导致制动鼓面临三重腐蚀威胁:化学腐蚀、电化学腐蚀和机械磨损的三重叠加效应,数据显示,在连续作业200小时后,普通制动鼓的径向跳动值可增加0.15mm,动平衡量损失达35%以上。
星申动技术团队通过2000余组对比实验发现,泥水残留物在制动鼓表面形成的腐蚀层具有明显的"梯度腐蚀"特征,表层0.2mm范围内以FeOOH为主的腐蚀产物,中层0.5mm区域呈现Fe3O4与Fe2O3的混合结构,深层则出现FeCO3晶间腐蚀,这种复合腐蚀结构不仅改变零部件质量分布,更会形成局部应力集中点。
预处理方案的技术创新
针对上述问题,星申动研发的"三阶九步"预处理方案包含三大核心技术模块:
1、无损清创技术
采用自主研发的脉冲式空化射流设备,通过调节0.5-2.5MPa的水压梯度,实现逐层剥离而不损伤基体,配合pH值9.2的碱性清洗剂,有效去除90%以上的硅酸盐沉积物,经测试,该工艺可将表面粗糙度控制在Ra3.2μm以内,为后续工序奠定基础。
2、腐蚀层量化分析
运用激光诱导击穿光谱(LIBS)技术,建立三维腐蚀图谱,通过采集500-900nm波段的光谱数据,精确识别腐蚀产物的成分分布,结合有限元分析软件,构建包含材料损失量、密度变化、应力分布等12项参数的修正模型。
3、动态补偿算法
开发基于机器学习的自适应平衡算法,该算法能根据实时检测的32组传感器数据,动态调整补偿方案,在实际应用中,系统可自动识别0.01g·mm的微小失衡量,并通过矢量叠加原理实现多平面自动补偿。
工程实践与效益分析
在湖北荆门某农机合作社的验证项目中,应用该方案的25台拖拉机展现出显著优势,对比传统工艺,制动鼓使用寿命延长2.3倍,平衡校正效率提升60%,单台设备年维护成本降低4200元,更关键的是,将制动系统的故障间隔时间从150小时提升至500小时。
技术总监李明华介绍:"我们的预处理方案不是简单的表面处理,而是建立在对材料失效机理的深度解析之上,通过构建腐蚀-应力-振动的耦合模型,实现了从被动维修到主动预防的技术跨越。"
行业标准与未来发展
星申动正牵头制定《农用机械制动系统泥水工况适应性技术规范》,该标准首次将"预处理工序"纳入制动鼓生产工艺流程,标准草案中明确规定:对于水田作业机械,制动鼓应预留0.3-0.5mm的腐蚀补偿余量;平衡校正需考虑泥水残留物的质量分布影响因子。
在智能化升级方面,企业正在测试集成物联网技术的第五代平衡机,该设备可通过5G模块实时上传工况数据,结合数字孪生技术实现远程诊断,测试数据显示,新系统可将平衡校正精度提升至G0.4级,达到航空发动机转子的平衡标准。
从江汉平原到三江湿地,星申动的技术团队持续破解着中国农业机械化进程中的现实难题,其创新实践表明:解决农机制造领域的"卡脖子"问题,需要将基础研究与工程应用深度结合,在乡村振兴战略背景下,这种以实际问题为导向的技术创新,正为农业装备的转型升级注入新的动能,正如企业创始人张建国所言:"农机设备的每一个振动异常,都可能影响粮食生产的每一粒收获,我们用毫米级的精度守护着中国农业的现代化进程。"