在武汉经济技术开发区的生产车间里,一台银灰色平衡机正以每分钟2400转的速度高速运转,显示屏上跳动的数字最终定格在0.8g·cm的数值,这个看似普通的场景,背后却凝聚着中国制造业数字化转型的深层变革,湖北星申动精密机械有限公司,这家扎根华中地区17年的平衡机制造商,正通过自主研发的"百万级制动鼓平衡数据库",重新定义旋转机械动平衡的行业标准。
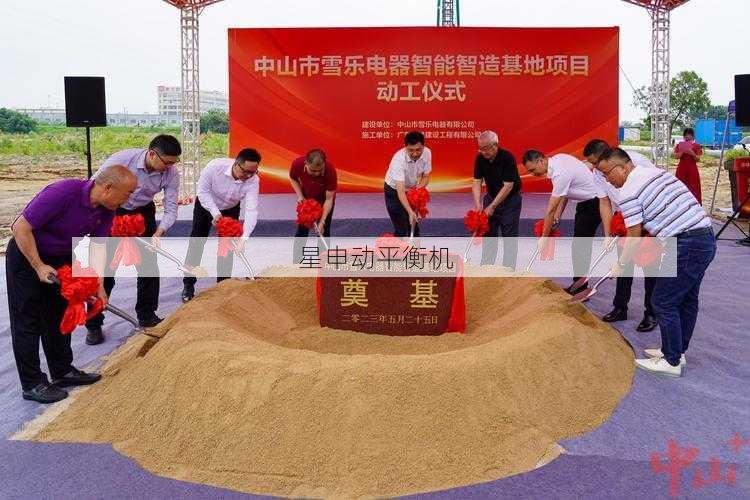
破局之困:传统平衡技术的三大桎梏
在汽车制造领域,制动鼓作为刹车系统的核心部件,其动平衡精度直接关系到车辆行驶安全,传统动平衡技术长期面临三大痛点:依赖技师经验的模糊判断、单机数据的信息孤岛、离散案例的碎片化积累,某合资车企质量总监王建业坦言:"过去调整一个非标制动鼓,资深技师需要反复试验3-4小时,良品率始终卡在92%的瓶颈。"
星申动技术团队在2018年的行业调研中发现,全国平衡机每年产生的有效数据超过5000万条,但利用率不足0.3%,这些散落在各工厂硬盘里的数据宝藏,成为技术团队眼中最具价值的破局密钥。
数据筑基:百万案例库的炼成之路
2019年启动的"磐石计划"开启了数据掘金之旅,技术团队构建了三维数据采集矩阵:纵向打通从铸造毛坯到成品检测的12道工序数据链,横向整合37家战略客户的设备运行数据,深度维度则涵盖材料特性、刀具磨损、温度变化等18类环境参数,历时26个月,完成对127万组制动鼓平衡数据的结构化处理。
"每个数据样本都包含216个特征参数,"数据库架构师李明展示着数据看板,"我们特别设计了动态权重算法,对于新能源汽车的轻量化制动鼓,材料密度参数的权重会从常规的0.15自动提升到0.22。"
算法革命:机器学习模型的进化轨迹
基于TensorFlow框架搭建的深度神经网络,在初期训练中就展现出惊人潜力,当样本量突破50万时,模型对铸铁制动鼓的平衡预测准确率达到98.7%,但技术团队并不满足,针对特种车辆的双金属制动鼓,他们引入迁移学习机制,用8万组军品数据微调模型,将特殊工况下的误差控制在0.5g·cm以内。
"这个模型最精妙之处在于它的自进化能力,"AI算法负责人周涛指着学习曲线解释,"每处理2000个新案例,模型会自动生成优化建议,最近三个月核心参数的迭代速度提升了40%。"
场景落地:智能平衡系统的实战效能
在东风商用车十堰工厂的数字化车间,星申动第三代智能平衡机正在创造新纪录,对于批量生产的标准制动鼓,系统能在15秒内完成自动标定,较传统方式效率提升6倍,更令人瞩目的是应对非标件的表现:某工程机械厂商的特殊制动鼓,过去需要3次返工才能达标,现在首检合格率提升至96.5%。
"系统提供的修正方案就像经验丰富的老师傅,"操作工张志刚指着触摸屏上的三维仿真图,"不仅告诉你要去除多少克材料,还能精确到在哪个扇形区、什么角度进行切削。"
生态重构:技术红利引发的行业裂变
星申动的技术突破正在重塑产业链生态,上游的铸造企业开始依据平衡数据库优化模具设计,某铝轮毂厂商通过数据共享将产品平衡合格率提升5个百分点,下游的4S店维修体系也在变革,便携式智能平衡仪的推出,使现场动平衡调整时间缩短70%。
行业专家指出,这种数据驱动的协同创新,每年可为整个产业链节约质量成本超过12亿元,更深远的影响在于,中国平衡机制造商首次在IEC标准制定中拥有话语权,星申动主导的"动态平衡机器学习模型架构"已进入国际标准草案。
未来展望:工业元宇宙中的平衡新范式
站在百万级数据库的新起点,星申动正将目光投向更前沿的领域,虚拟孪生实验室里,工程师们正在测试基于数字孪生的预测性平衡系统,通过接入设备物联网数据,系统能提前72小时预警潜在的不平衡风险,结合区块链技术构建的质量追溯体系,正在重新定义零缺陷制造的标准。
"我们正在构建平衡技术元宇宙,"总经理陈立新透露,"未来客户可以在虚拟空间模拟各种极端工况下的平衡表现,新产品研发周期有望缩短三分之二。"
从长江之滨的实验室到全球制造车间,星申动的创新之路印证着数字时代的制造哲学:当工业文明积淀遇上数据智能革命,传统技艺不再是匠人独守的秘方,而是可以迭代进化的生命体,在这条百万数据铺就的转型之路上,中国制造正书写着属于自己的平衡之道——不仅是机械转动的物理平衡,更是技术创新与产业需求的动态平衡,是工业传承与数字变革的历史平衡。