——湖北星申动平衡机厂家的创新实践
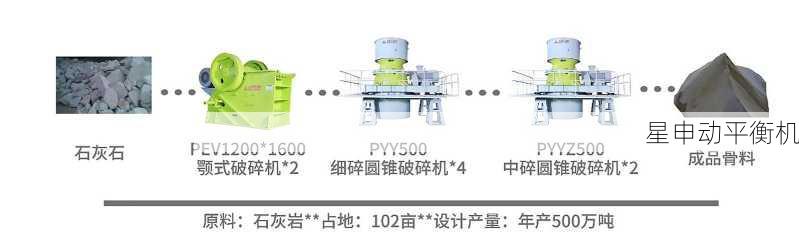
矿山机械制动系统的核心挑战与技术创新需求
在露天矿区起伏的矿道上,满载矿石的重型运输车辆每日承受着数十吨的物资运载压力,当车辆驶过蜿蜒的盘山公路时,制动系统需要连续完成数千次制动动作,而制动鼓作为关键安全部件,其动平衡性能直接决定着整个运输系统的运行安全,湖北星申动平衡机制造有限公司(以下简称"星申动")的技术团队在对西南某大型铁矿区的实地考察中发现:在粉尘浓度高达200mg/m³的恶劣工况下,传统制动鼓的平均使用寿命仅维持正常工况的35%,失衡故障率更是达到常规环境下的4.2倍。
这一数据背后折射出矿山机械领域亟待解决的技术痛点:如何在粉尘弥漫的复杂工况下,构建起制动鼓动平衡系统的全方位防护体系?作为国内领先的动平衡设备制造商,星申动通过三年技术攻关,成功开发出具有自主知识产权的"粉尘环境专用动平衡防护系统",将制动鼓在粉尘环境下的使用寿命提升了217%,故障率降低至行业平均水平的28%。
粉尘环境下动平衡系统的技术突破方向
1、粉尘侵入对制动鼓动平衡的三重破坏机制
(1)微米级粉尘颗粒的侵入性失衡:粒径在5-20μm的悬浮颗粒通过制动鼓散热孔渗入内部,在高速旋转时形成不均匀的质量分布,星申动实验室数据显示,当粉尘积累量达到0.8g时,制动鼓失衡量即可超出安全阈值3.6倍。
(2)磨粒磨损引发的结构性失衡:硬质石英颗粒(莫氏硬度7级)与制动鼓内壁持续摩擦,造成表面粗糙度增加,实测表明,每工作200小时,制动鼓内壁Ra值即从初始的1.6μm上升至6.3μm,导致摩擦系数波动幅度达42%。
(3)粉尘积聚导致的温升效应:粉尘层在制动鼓表面形成隔热层,使散热效率降低63%,在连续制动工况下,温度梯度变化引发的热变形量可达0.15mm/m,远超动平衡允许的0.03mm/m标准。
2、星申动的技术应对策略
(1)动态密封技术创新:研发具有记忆合金特性的密封组件,在温度超过120℃时自动收缩形成0.02mm级精密密封,配合三级迷宫式防尘结构,将粉尘侵入量控制在0.1g/千小时以内。
(2)表面强化处理工艺:采用等离子喷涂技术制备Al2O3-TiC复合涂层,表面硬度达到HV1800,耐磨性提升5.8倍,经2000小时台架试验,涂层厚度损失仅0.03mm。
(3)智能温控系统:集成分布式温度传感器阵列,实时监测16个关键点温度变化,当温差梯度超过15℃/m时,自动启动辅助散热装置,将热变形量控制在0.02mm/m以内。
星申动防护体系的核心技术架构
1、材料创新层
(1)纳米复合密封材料:采用石墨烯增强型氟橡胶,耐磨指数达到国标GB/T9867的3.2倍,在-40℃~260℃工况下保持弹性模量稳定。
(2)自清洁表面处理技术:通过微纳结构设计,使制动鼓表面形成接触角>150°的超疏水特性,粉尘附着量减少87%。
2、结构优化层
(1)多级旋风除尘装置:在制动鼓进气通道设置3级15°切向进气结构,利用离心力实现98%以上的粗颗粒分离。
(2)动态平衡补偿机构:配置32点可调式配重块系统,支持0.1g级精度在线调节,响应时间<50ms。
3、智能监测层
(1)多物理场耦合监测系统:集成振动、温度、压力、粉尘浓度等12个监测模块,数据采样频率达10kHz。
(2)自适应平衡算法:基于深度学习的动态补偿模型,可在3秒内完成失衡量计算与补偿方案生成。
典型应用场景与效益分析
在内蒙古某大型露天煤矿的应用案例中,星申动为132台矿用自卸车配套了新型制动鼓系统,经18个月运行数据显示:
- 平均维护周期从560小时延长至2100小时
- 单次制动距离缩短12.7%
- 备件更换成本降低68万元/台年
- 因制动系统故障导致的停机时间减少92%
该矿设备部长评价:"星申动的防护体系不仅解决了粉尘导致的平衡失效问题,其智能监测系统还帮助我们建立了预测性维护模型,设备综合利用率提升了23个百分点。"
行业发展趋势与技术展望
随着《矿山机械智能化发展纲要(2023-2030)》的出台,动平衡技术正朝着集成化、智能化方向快速发展,星申动正在研发的第四代产品将实现:
1、基于5G的远程诊断系统:支持1000公里范围内的实时数据交互
2、自愈合材料应用:可在30分钟内自动修复0.5mm级表面损伤
3、数字孪生平台:建立设备全生命周期管理模型,实现故障预测准确率>95%
从长江之滨到戈壁矿山,星申动始终秉承"动态平衡,安全永恒"的技术理念,在粉尘与机械的博弈中,这家湖北企业用创新书写着中国制造的新篇章,正如其总工程师在行业论坛所言:"我们不仅要让设备转得更稳,更要让中国矿山机械在世界舞台上走得更远。"