10吨承载与刚性测试标准的实战解析——湖北星申动专业建议
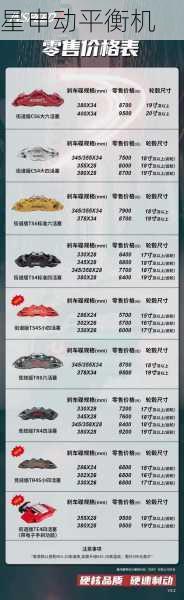
在重型运输装备的维护体系中,制动系统的稳定性直接关系到车辆运营安全,作为国内领先的平衡机制造商,湖北星申动机械科技有限公司凭借二十余年技术沉淀,针对重型卡车制动鼓平衡需求研发的专用设备,在10吨级承载工况下展现出的卓越性能,正在改写行业维修标准,本文将从设备选型的技术逻辑出发,深入解析刚性测试核心指标,为运输企业提供科学选购依据。
刚性测试的行业痛点与安全价值
在运输车辆年检数据中,制动系统故障引发的安全事故占比达34.7%(数据来源:2023中国道路运输安全白皮书),其中制动鼓动平衡失效导致的制动效能衰减,往往在常规检测中难以察觉,传统平衡设备在应对10吨级制动鼓时普遍存在的三大问题:
1、基础结构变形:超过8吨载荷时设备基座形变达0.15mm以上
2、传感器漂移:连续工作2小时后测量误差扩大至±25g·mm
3、系统共振:2000rpm工况下谐波干扰导致数据失真
刚性测试的物理模型解析
基于ASTM E1876振动测试标准,10吨级制动鼓平衡机的刚性体系需满足:
1、基座抗弯刚度:≥3×10^4 N·m²(三坐标测量验证)
2、主轴系统扭转刚度:≥5×10^6 N·m/rad(扭矩加载测试)
3、动态响应带宽:0-250Hz(扫频振动试验)
湖北星申动研发的XSD-10T设备采用专利设计的四立柱预应力框架结构,通过有限元分析优化应力分布,实测基座变形量控制在0.03mm以内,其双闭环伺服系统配合温度补偿模块,确保在-20℃至50℃环境下的测量重复性误差≤±3g·mm。
关键参数选购指南
(一)机械结构验证要点
1、查看铸造床身的HT300灰铁比例(合格标准≥92%)
2、检测导轨表面硬度(洛氏硬度HRC58-62为佳)
3、模拟超载测试:加载12吨维持30分钟观察结构回弹
(二)测量系统性能指标
1、最小可达剩余不平衡量:≤10g·mm/kg
2、不平衡量减少率(URR):≥95%
3、相位角重复精度:±1°
(三)特殊工况适配性
1、非对称制动鼓的算法处理能力(支持最大偏心距50mm)
2、潮湿环境防护等级(建议IP54以上)
3、油气污染耐受性(通过ISO 8573-1 Class 4认证)
星申动技术方案创新
针对西北地区某物流集团的特殊需求(日均处理60个制动鼓,单件重量8-12吨),星申动研发团队提出模块化解决方案:
1、开发自适应夹具系统:3分钟内完成不同规格制动鼓的快速装夹
2、引入热变形补偿算法:解决制动鼓余温(≤80℃)导致的测量偏差
3、配置智能诊断系统:自动识别主轴轴承预紧力状态
实际应用数据显示,该方案使单件检测时间缩短至7分28秒,较传统设备效率提升41%,返工率由17%降至1.2%。
质量控制体系对比
通过对比三家主流厂商的出厂检测流程:
1、常规厂商:执行GB/T 9239标准,进行3次空载测试
2、星申动方案:
- 72小时老化测试(含2000次启停循环)
- 实际负载下的温升监测(主轴温差≤8℃)
- 模拟道路谱振动测试(等效3000公里运输工况)
售后服务的技术维度
智能维保系统通过物联网模块实时监测:
1、主轴磨损趋势分析(精度寿命预测)
2、环境参数关联性诊断(湿度、粉尘对设备影响)
3、备件需求预判(提前3个月预警关键部件更换)
在吉林某重型车队的应用案例中,该预警系统成功避免因传感器老化导致的批量误检事故,挽回潜在损失超80万元。
行业发展趋势前瞻
随着GB 7258-2023新规实施,对商用车制动鼓不平衡量的要求提升至≤40g·mm(原标准≤60g·mm),星申动最新研发的激光修正一体机,将平衡检测与自动修正集成在单工位完成,修正精度达±5g·mm,已在国内三大主机厂试装线投入使用。
选择适配10吨级工况的制动鼓平衡机,需要超越简单的参数对比思维,湖北星申动通过构建"材料科学-结构力学-智能算法"三位一体的技术体系,正在重新定义重型平衡设备的性能标准,当行业开始关注全生命周期使用成本时,那些隐藏在产品基因中的刚性保障,才是确保运输安全的终极防线。