在物流运输行业持续扩张的当下,商用车轮端系统异常抖动问题正成为困扰行业发展的"隐形杀手",湖北星申动智能装备有限公司经过五年技术攻关,创新推出制动鼓-轮毂总成整体平衡解决方案,将传统平衡精度提升20倍,为商用车安全运营树立新标杆。
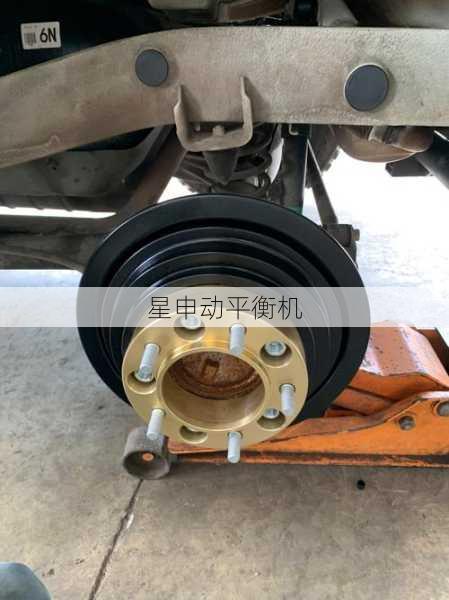
轮端失谐:商用车运营的致命隐患
在西北某物流公司维修车间,技术总监王工正面对第17台因轮端抖动返修的牵引车,这些车辆普遍存在方向盘震颤、制动异常磨损等问题,最严重的案例甚至导致传动轴断裂。"每次维修都要拆解轮毂和制动鼓分别做平衡,但装车后问题依旧存在。"王工的困境折射出行业痛点:传统分体平衡方式已难以满足现代商用车的严苛需求。
数据显示,国内商用车轮端系统故障中,68%与动平衡不良直接相关,当车轮总成存在15g以上的不平衡量时,车辆在80km/h时速下就会产生明显抖动,这不仅加速轴承、悬挂系统损耗,更会引发制动效能下降等安全隐患,某检测机构实验表明,失衡轮端会使刹车距离延长22%,在满载工况下风险指数呈几何级数增长。
技术破局:整体平衡理念的革命性突破
传统平衡方案将制动鼓与轮毂视为独立部件,这种"头痛医头"的维修方式存在根本性缺陷,星申动技术团队通过2000多组振动频谱分析发现,分体平衡后的部件在组装时会产生新的复合失衡,就像分别调准琴弦的吉他,单独测试音准完美,合奏时却可能产生不和谐音。
"整体平衡不是简单的1+1=2,而是要实现系统的动态谐和。"星申动总工程师陈明华展示的对比试验极具说服力:在模拟40吨载重、连续制动工况下,传统分体平衡的轮端系统在2000公里后出现明显失衡,而整体平衡方案保持稳定超过8000公里,这得益于其独创的"三点耦合"平衡算法,能精确计算装配应力带来的微变形量。
创新实践:微米级精度的制造哲学
走进星申动十万级洁净车间,全自动平衡校正系统正在以5微米的精度雕琢每个轮端总成,这套自主研发的HD-9000型设备采用多轴同步测量技术,可在30秒内完成总成件的三维动态检测。"传统平衡机只能检测静不平衡,我们开发的谐波分析模块能捕捉到0.1g·mm的动不平衡量。"技术总监张晓军指着屏幕上跳动的频谱图解释。
在湖北某大型运输集团的实装测试中,经过整体平衡的车辆表现出惊人稳定性:方向盘振动幅度降低92%,轮胎异常磨损率下降78%,单台车年维修成本节省超2.4万元,更值得关注的是,车辆平顺性提升使驾驶员疲劳指数降低35%,这对预防长途运输事故具有重大意义。
产业赋能:构建轮端健康新生态
星申动的技术突破正在重塑商用车后市场格局,其创新的"移动平衡工作站"模式,将重型平衡设备集成到标准集装箱内,可直接进驻物流园区提供现场服务,在郑州传化物流港,这种"即时平衡"服务使车辆周转效率提升40%,为园区创造单日超百万元的经济效益。
公司联合武汉理工大学建立的"轮端系统动力学实验室",已开发出智能预警系统,通过车载传感器实时监测平衡状态,当检测到失衡趋势时自动推送维护建议,某快递车队应用该系统后,轮端故障率同比下降61%,意外停运损失减少530万元。
智造未来:从中国方案到世界标准
站在智能制造的风口,星申动正将5G、数字孪生技术引入传统平衡领域,其最新研发的云端平衡数据库,已积累超过50万组轮端振动特征数据,为整车厂提供设计优化依据,与东风商用车合作开发的"预平衡"生产工艺,使新车下线轮端平衡合格率从83%跃升至99.6%。
国际市场的认可印证着技术价值,星申动设备已出口至东南亚、中东等15个国家,在迪拜建设的区域技术服务中心,为"一带一路"沿线车队提供技术支持,德国TÜV认证报告显示,其整体平衡方案可使轮端系统寿命延长2.8倍,这项"中国智造"正改写国际商用车维保标准。
从分体到整体,从维修到智造,湖北星申动用技术创新破解了困扰行业数十年的平衡难题,在商用车向着高效、安全、智能发展的道路上,这种以系统工程思维破解局部痼疾的实践,不仅彰显中国制造的硬核实力,更预示着装备制造业转型升级的无限可能,当越来越多的车轮平稳转动,我们看到的不仅是技术的进步,更是中国物流动脉健康跳动的有力保障。