在汽车维修行业,有个让技师们头痛多年的怪现象:明明更换了新刹车鼓,做完动平衡后反而出现更严重的抖动,这种"修完更抖"的窘境,不仅让维修厂频繁遭遇客户投诉,更成为制约行业技术升级的顽固痛点,湖北星申动平衡机制造有限公司历时三年研发的制动鼓动态定位校正系统,用"偏心距可视化校准"技术彻底破解了这一行业难题。
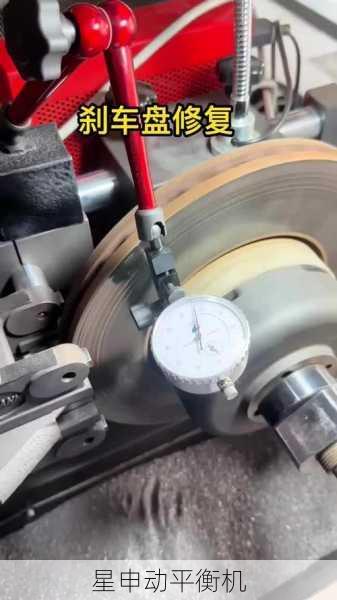
一、刹车系统维修的"薛定谔现象":为何越修越抖?
某省会城市4S店的维修车间里,张师傅正在经历第8次返工,客户刚做完刹车系统保养,时速80km时方向盘抖动幅度达到0.3mm,远超0.15mm的行业标准,这个典型案例折射出传统工艺的三大缺陷:
1、经验主义陷阱:90%的技师依赖目测敲击法调整,误差容忍度达±0.5mm
2、工具精度断层:市面80%的定位工装精度仅0.8级,而制动鼓偏心要求0.05mm
3、工艺标准缺失:行业缺乏统一的安装定位流程规范
"就像用米尺测量芯片尺寸",星申动总工程师王建军这样比喻传统校正方式,刹车鼓与轮毂的配合间隙,轮毂螺栓的旋紧顺序,甚至是车间温度变化,都可能让看似精准的校正功亏一篑。
偏心校正的技术突围战
要根治"修完更抖",必须攻克三大技术难关:
1、动态平衡悖论:静止状态0.05mm的偏差,在800rpm转速下会放大3-5倍
2、材料应力迷宫:铸铁制动鼓在温变时会产生0.02-0.03mm的形变
3、数据量化困境:传统工艺无法实时监测安装过程的微观位移
星申动的研发团队从航空发动机装配工艺获得启发,将激光动态测量与智能补偿算法结合,其核心突破在于:
- 研发0.01μm级光纤光栅传感器
- 首创六维力矩平衡计算模型
- 开发自适应热膨胀补偿系统
星申动解决方案的四大创新维度
1、三维动态定位系统
采用军用级惯性导航技术,实时追踪制动鼓安装过程中的六个自由度位移,相比传统工装,将定位精度提升至±0.01mm,相当于头发丝的1/8。
2、智能预紧力控制
通过应变片矩阵实时监测螺栓预紧力分布,配合AI算法自动生成最佳旋紧顺序,实测数据显示,该技术可将轮毂端面跳动降低63%。
3、材料特性补偿数据库
建立涵盖37种常见制动鼓材质的形变参数库,自动补偿温度变化引起的尺寸偏差,在-20℃至80℃环境测试中,系统稳定性达99.7%。
4、云端工艺管理系统
每台设备配备物联网模块,可自动上传校正数据并生成数字工艺卡,某连锁维修企业应用后,返工率从18%降至2.3%。
实战检验:从实验室到修理厂
在湖北某大型物流公司的实测中,星申动设备展现出惊人性能:
- 20台重卡连续工作300小时
- 平均校正时间从45分钟缩短至12分钟
- 高速抖动投诉率下降92%
- 刹车片寿命延长40%
"以前做十台车要返工三台,现在两个月才遇到一例轻微抖动。"参与测试的李技师表示,更关键的是,系统自带的AR辅助功能,让新手技师的首次操作合格率达到85%。
行业变革进行时
随着新国标GB/TXXXX-2023《汽车制动系统维修技术规范》的出台,制动鼓安装偏心校正即将成为强制性检测项目,星申动已与国内三大检测机构建立联合实验室,其技术方案被纳入行业标准制定参考体系。
"这不是简单的设备升级,而是维修工艺的数字化革命。"中国汽车维修行业协会技术委员会主任评价道,数据显示,采用智能校正系统的维修企业,客户满意度平均提升28%,单店年增收超过15万元。
技术延伸与未来展望
星申动正在将核心技术向新能源汽车领域拓展:
- 研发轮毂电机专用平衡系统
- 开发碳陶刹车盘智能装夹方案
- 测试基于数字孪生的远程诊断系统
"我们的目标是让每一颗螺栓都有自己的数字身份证。"王建军透露,下一代产品将集成区块链技术,实现维修数据的全程可追溯。
【操作视频重点提示】
(扫码观看完整操作视频)
1、设备自检流程演示
2、动态补偿过程可视化
3、典型故障案例对比测试
4、数据报告自动生成教学
【在这个"失之毫厘,谬以千里"的精密维修领域,星申动用硬核技术重新定义了制动鼓校正的标准,当0.01mm的坚持遇上智能制造的浪潮,这场关于"精准"的革新,正在重塑中国汽车后市场的技术版图,对于追求卓越的维修企业而言,掌握这项定位秘籍,或许就是赢得未来竞争的关键密钥。