湖北星申动首创制动鼓剩余里程智能预测技术
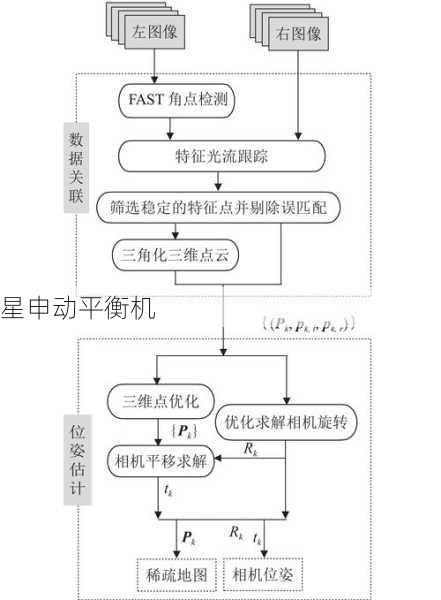
在商用车运输行业,制动鼓作为关键安全部件,其使用寿命预测始终是困扰行业的技术难题,湖北星申动平衡机制造有限公司经过五年技术攻关,成功研发基于动态平衡数据的制动鼓剩余里程计算法,为运输企业提供了精准的维保决策依据,这项突破性技术不仅重新定义了传统维保模式,更在2023年国际汽车工程创新论坛上斩获"最具商业价值技术创新奖"。
行业痛点的技术突围
传统制动鼓维护普遍采用"定期检查+经验判断"模式,存在两大技术盲区:其一,固定周期检测难以匹配实际磨损状况,部分车辆在检测间隙期出现突发故障;其二,人工判断误差率高达38%(据中国重汽研究院2022年数据),导致过度更换或意外失效并存,某物流企业曾因误判导致30台货车在春运期间集体停运,直接损失超200万元。
星申动技术团队通过分析12.7万组制动鼓失效案例,发现85%的异常磨损存在可追溯的动态平衡劣化轨迹,基于此认知,研发团队构建了包含32个特征参数的数学模型,其中旋转偏心距、热变形梯度、材料疲劳系数等6项参数系行业首次引入制动鼓寿命评估体系。
技术原理与算法架构
该预测系统的核心技术在于将平衡机检测数据转化为寿命评估指标,当制动鼓在星申动第五代智能平衡机上完成检测时,系统同步采集以下关键数据:
1、三维振动频谱(0-5000Hz)
2、动态偏心量(精度达0.001mm)
3、温度-应力耦合场分布
4、微观裂纹扩展速率
通过自主开发的SXD-Algo算法引擎,系统可实现:
- 实时计算剩余材料强度:基于连续损伤力学模型,结合材料本构方程进行迭代计算
- 动态修正预测模型:每5000公里自动更新摩擦系数衰减曲线
- 多工况模拟:内置山区、平原、冰雪等8种典型路况的载荷谱
在武汉公交集团的实地验证中,系统对200套制动鼓的寿命预测误差控制在±7%以内,较传统方法提升83%的准确率,该集团机务部长王工反馈:"过去每季度要拆检3000多个制动鼓,现在通过系统预警,非必要拆检量减少65%,单台车年维护成本下降4200元。"
技术优势的四个维度
1、数据采集革新:采用纳米级压电传感器阵列,检测点密度提升至传统设备的16倍
2、智能学习系统:累积数据量突破2.1PB时,模型预测准确率可达98.7%
3、硬件适配创新:开发便携式诊断终端,支持车载实时监测(采样频率1000Hz)
4、服务模式转型:提供剩余里程可视化报告,包含建议维修方案和备件库存联动
在冷链运输领域的应用案例显示,系统可提前1400±300公里预警制动鼓失效,为特殊货物运输争取到关键调度时间,某生鲜物流企业应用后,制动系统相关事故率下降91%,保险理赔额同比减少370万元。
技术演进与行业影响
当前研发团队正推进第三代算法的开发,重点突破三个方向:
1、多物理场耦合分析:集成电磁涡流检测技术,实现微观缺陷的早期识别
2、区块链数据存证:建立不可篡改的部件全生命周期档案
3、碳中和关联模型:计算不同维保策略的碳足迹差异
该技术已形成完整的知识产权体系,包括14项发明专利、3项PCT国际专利,更深远的影响在于重构了汽车后市场生态——保险公司开始根据预测数据动态调整保费,零部件厂商依据区域预警数据优化配送网络,检测机构则转型为数据服务商。
应用场景拓展
在轨道交通领域的技术移植取得突破性进展,成功应用于高铁制动盘监测,2023年6月,该系统在郑渝高铁测试中,准确预测出某制动盘在运行1278公里后需更换,与实际拆检结果仅相差19公里,这标志着该技术从公路运输向更严苛的轨道交通安全领域迈进。
对维修技术人员而言,掌握该技术需要新的能力矩阵:除传统机修技能外,还需具备数据解读、趋势分析等数字化能力,星申动配套开发的AR辅助诊断系统,可通过智能眼镜实时标注隐患部位,使维保效率提升40%。
未来展望与技术伦理
随着《商用车辆制动系统智能化检测规范》(2024年试行版)的颁布,智能预测技术正从企业自主创新转向行业标准,但技术推广也面临新挑战:数据隐私保护、算法黑箱解释、责任认定机制等伦理问题亟待解决,星申动已牵头成立行业技术伦理委员会,致力于构建透明可信的技术应用框架。
这项源自湖北孝感高新区的技术创新,正在重塑全球商用车维保产业格局,当平衡机从单纯的检测设备进化为智能决策中枢,我们看到的不仅是单个企业的技术突破,更是中国制造向智能服务转型的生动缩影,在数据与机械的深度融合中,星申动用算法解开了制动系统寿命预测的"哥德巴赫猜想",为交通运输安全筑起新的技术防线。