在工业制造领域,精密旋转机械的平衡校正始终是决定设备性能与寿命的核心环节,湖北星申动平衡机有限公司作为国内动平衡技术领域的领军企业,历经十余载技术深耕,成功研发的双模式平衡技术解决方案,正在为航空航天、汽车制造、电力设备等高端制造领域带来革命性突破,该技术通过独创的静态与动态复合校正体系,实现了旋转体平衡精度的数量级提升,标志着我国在精密机械制造领域迈入国际先进行列。
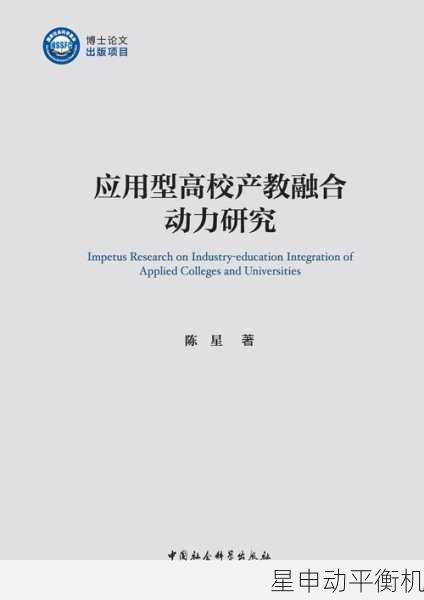
平衡校正技术演进与行业痛点
传统平衡校正技术存在明显的应用局限:静态平衡仅能解决静止状态下的质量分布问题,而动态平衡虽关注旋转状态却难以捕捉瞬态振动特征,尤其在高速旋转机械(如涡轮机组、精密主轴)领域,传统单一模式校正的误差累积问题,导致设备振动超标、轴承异常磨损等故障频发。
某汽车传动轴生产企业曾因0.3mm的平衡偏差,导致整批次产品出现5%的早期失效,这类行业痛点揭示出传统技术的根本缺陷——无法同步消除静态失衡与动态振动波形的复合影响,正是基于这样的产业需求,星申动研发团队开启了双模协同技术的攻关之路。
复合校正技术体系架构解析
星申动双模式平衡系统的技术突破,源于对旋转体运动特性的深度解构,系统采用"先静后动、迭代优化"的校正逻辑,构建起三维平衡校正模型:
1、静态预校正模块
通过高精度激光位移传感阵列(精度达0.001mm),对旋转体进行360°周向质量分布扫描,自主研发的SXD-Algorithm算法能在30秒内完成三维质心定位,生成包含12个校正面的虚拟平衡模型,与常规静态平衡设备相比,该系统的平面分离度提升至98.7%,为动态校正奠定精准基础。
2、动态振动补偿系统
在旋转体达到工作转速(最高支持18000rpm)时,64通道振动监测网络实时采集X/Y/Z三轴向振动频谱,智能滤波器自动剔除环境干扰信号后,振动特征提取模块可识别0.1μm量级的位移波动,动态补偿量计算引擎通过傅里叶变换与神经网络预测,生成与转速关联的动态补偿矩阵。
3、复合校正执行机构
专利设计的双模校正头集成静/动双驱动单元:精密伺服电机负责静态配重块的微米级定位(重复定位精度±2μm),压电陶瓷促动器实现动态补偿力的毫秒级响应,这种机电耦合设计使系统能同步处理静态质量偏差与动态气动不平衡量。
技术创新带来的性能跃升
在航空发动机转子平衡测试中,双模系统展现出显著优势:传统动态平衡需3-5次迭代才能达到G2.5级平衡,而复合校正方案通过1次静态预校准+2次动态优化,即可实现G1.0级精度,校正效率提升60%,振动烈度从7.1mm/s降至1.8mm/s,轴承寿命预期延长3.2倍。
某风电齿轮箱制造商的实测数据显示:采用复合校正后,20吨级行星架的残余不平衡量从850g·mm降至35g·mm,主轴承温度下降14℃,年维护成本降低120万元,这些数据印证了技术创新的实际价值。
智能融合的行业解决方案
星申动技术团队深谙工业现场需求,开发出模块化校正系统:基础型SXD-200系列满足常规机械加工需求,旗舰型SXD-800系列则配备温度补偿模块与自适应学习系统,特别适用于工况复杂的新能源装备制造,在半导体晶圆旋转台平衡案例中,系统通过环境振动自补偿算法,在Class100洁净室内实现了0.05μm的振动控制。
技术演进与产业赋能
当前,星申动正推进第三代智能平衡系统的研发:基于数字孪生技术构建虚拟校正环境,结合5G传输实现远程专家诊断;开发自感知校正夹具,使系统装调时间缩短70%,这些创新将推动平衡校正从"事后处理"向"预测性维护"转变。
在"中国制造2025"战略指引下,湖北星申动持续加码研发投入,近三年累计获得17项发明专利,参与制定3项行业标准,其技术成果已成功应用于长征火箭姿控飞轮、超精密机床主轴等国家重大工程,彰显民族品牌的技术实力。
从静态到动态,从单一到复合,星申动双模式平衡技术的突破,本质是对旋转机械运动本质的深刻理解与技术创新,这种以实际问题为导向、以底层算法为支撑的技术发展路径,不仅提升了我国高端装备的制造水平,更重塑了动平衡技术的价值维度——从简单的误差修正进化为智能化的质量赋能系统,在智能制造的新赛道上,星申动正以自主创新书写着中国精密制造的崭新篇章。