在武汉经济技术开发区的一间现代化车间里,一台台银灰色的制动鼓正以每分钟2500转的速度高速旋转,操作屏上跳动的数字突然由绿转红,远在深圳的技术团队立即收到预警信息,三分钟内就完成了异常参数诊断——这是湖北星申动机械有限公司最新投入市场的5G智能平衡检测系统创造的工业物联新场景。
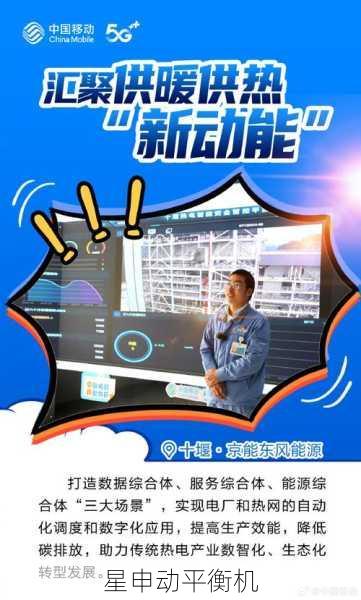
传统检测遭遇转型阵痛
作为汽车核心安全部件的制动鼓,其动平衡精度直接影响着车辆制动效能,传统检测流程中,工人需要反复拆装试重块,单件检测耗时长达40分钟,且合格率仅能维持在92%左右,湖北三环车桥公司的质量总监李国雄坦言:"去年因制动鼓平衡问题导致的售后索赔就达370万元,这还不包括品牌信誉的隐性损失。"
行业痛点催生变革需求,星申动技术团队在走访36家汽配企业后发现,83%的厂商面临检测效率与精度的双重困境,传统设备的数据孤岛现象更让质量追溯举步维艰,正是在这样的背景下,5G远程诊断系统应运而生。
智能系统的技术突破
这套革命性系统的核心在于"端-边-云"协同架构,在设备端,高精度振动传感器和激光位移计的采样频率提升至10kHz,较传统设备提升8倍;边缘计算单元对原始数据进行降噪处理后,通过5G专网以20ms的延迟将数据包传输至云端。
"我们自主研发的平衡算法模型是关键突破。"星申动首席工程师王振华展示着系统后台,三维可视化界面上,每个制动鼓的偏心量、相位角等参数实时跳动。"系统可自动匹配38种材料特性数据库,结合深度学习模型,将平衡校正方案的准确率提升到99.6%。"
在东风商用车襄阳工厂的实际应用中,这套系统创造了行业新纪录:单个制动鼓检测时间压缩至12分钟,日均检测量提升至180件,更令人瞩目的是,系统积累的270万组检测数据正在训练新一代AI模型,为预测性维护提供支持。
云端协同重构产业生态
在武汉智能网联汽车测试场,技术人员向我们演示了远程诊断的完整流程,当某批次制动鼓出现质量波动时,云端平台不仅能即时推送修正方案,还能联动原材料供应商分析钢材批次特性,这种跨产业链的数据贯通,使得某物流企业的制动系统故障率同比下降67%。
"现在我们的服务半径从300公里扩展到全国。"星申动服务总监陈敏指着大屏上的运维地图介绍,系统上线半年已建立12个区域诊断中心,通过AR远程指导解决了83%的现场问题,湖北齐星集团设备科长赵伟算过一笔账:传统模式下每月需要3名专职维保人员,现在通过云平台管理,人力成本降低40%,设备综合效率(OEE)反而提升了15个百分点。
标准升级引领行业变革
随着国家机动车零部件质量监督检验中心的接入,这套系统正在催生新的行业标准,在最近的国家重点研发计划项目中,星申动牵头制定的《汽车制动部件智能检测规范》已进入征求意见阶段,中国汽车工业协会专家委员会主任董扬指出:"这种将过程数据转化为质量信用体系的做法,为行业数字化转型提供了可复制的样板。"
在江苏盐城新能源汽车产业园,搭载该系统的智能产线正在调试,项目负责人透露,通过与整车厂MES系统对接,制动鼓平衡数据将直接关联车辆VIN码,这意味着未来消费者扫码即可查看每个制动部件的"体检报告",这种全生命周期质量追溯模式,正在重新定义汽车零部件的价值维度。
站在布满数据流的监控大屏前,星申动总经理周明远描绘着更宏大的蓝图:"我们正在与北斗导航团队合作开发时空基准定位技术,计划明年推出亚微米级动态平衡检测系统。"在这个5G与工业互联网深度融合的新时代,这家湖北企业正以技术创新持续突破精密制造的边界,为中国智造注入澎湃动能。