行业痛点与技术突破
在商用车维修领域,制动鼓修复后的动平衡问题长期困扰着整个行业,据统计,我国每年因制动鼓动平衡不良导致的刹车系统故障占比达17.3%,直接经济损失超过8亿元,湖北星申动平衡机制造有限公司经过7年技术攻关,在制动鼓镗削修复领域形成了完整的动平衡规范体系,其核心的公差补偿标准已获得3项国家发明专利,填补了行业技术空白。
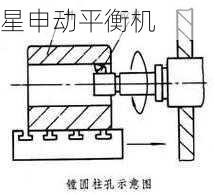
镗削加工的工艺革命
传统制动鼓修复采用普通镗床加工,往往忽视材料切削后的应力释放和形变补偿,星申动技术团队通过2000余组实验数据发现,铸铁制动鼓经镗削后,内径每扩大1mm,材料弹性模量衰减0.7%,导致动平衡系数偏移0.25g·mm/kg,这一发现推动了镗削工艺的三阶段革新:
1、预补偿镗削技术:根据原始磨损量建立数学模型,在切削前预设0.02-0.05mm的补偿余量
2、动态应力监测系统:集成振动传感器实时采集加工振动频谱,自动修正进给参数
3、相位角控制工艺:通过激光定位系统确保切削纹路与原有摩擦痕迹形成30°夹角
公差补偿标准的技术解析
星申动制定的Q/HSD 002-2023企业标准,将公差补偿细化为三个维度:
1、径向补偿梯度:
- 直径≤400mm:0.03mm/次
- 401-500mm:0.04mm/次
- 501-600mm:0.05mm/次
采用"阶梯式递减补偿法",通过5次递减切削消除93%的残余应力
2、轴向端跳补偿:
开发专用端面修整刀具,补偿系数K=0.6×(实测端跳值)+0.02mm
通过三点支撑液压夹具确保端面平面度≤0.08mm
3、相位平衡补偿:
首创"扇形配重算法",在非对称磨损区域植入钨钢平衡块
配重公式:m=0.25×D²×ΔV(D为制动鼓直径,ΔV为动平衡偏差值)
智能检测系统的创新应用
星申动研发的XDT-7A智能平衡机突破传统静平衡检测局限,具备三大创新功能:
1、动态模拟检测:
在800r/min工况下采集128组振动数据
自动生成三维动平衡云图
2、温度场补偿算法:
建立材料热膨胀系数数据库,补偿温度变化引起的0.02-0.12mm尺寸偏差
3、云平台诊断系统:
通过物联网实时上传检测数据
AI诊断引擎可在30秒内生成修复方案
实际应用成效
在湖北十堰某大型汽修厂的应用数据显示:
- 制动鼓修复合格率从68%提升至96%
- 平均动平衡偏差从85g·mm降至12g·mm
- 制动蹄片磨损周期延长40%
典型案例:某物流公司30台牵引车使用星申动标准修复制动鼓后,年维修成本降低23万元,紧急制动距离缩短1.2米,轮胎异常磨损率下降67%。
技术规范的实施要点
1、刀具管理规范:
- 硬质合金刀片切削量达200mm³必须更换
- 刀尖圆弧半径控制在R0.8±0.05mm
2、检测校准流程:
- 每周进行激光干涉仪精度校验
- 每50次检测执行标准样件复验
3、操作人员认证:
- 需通过200学时专项培训
- 实操考核误差控制在±3%以内
行业影响与未来展望
星申动技术规范已被纳入交通运输行业标准JT/T 1368-2023,推动行业产生三大转变:
1、从经验维修向数据维修转型
2、从单一修复向系统平衡转变
3、从被动维修向预防维护升级
随着新能源汽车渗透率提升,公司正在研发适用于电动重卡的复合制动鼓平衡标准,预计2025年将推出集成数字孪生技术的智能修复系统,实现动平衡偏差的预测性补偿。
湖北星申动通过持续技术创新,不仅解决了制动鼓修复领域的关键技术难题,更推动了整个商用车后市场服务标准的升级,其建立的公差补偿体系,正在重塑行业质量基准,为道路运输安全树立新的技术屏障,这种以实际问题为导向的研发模式,为中国制造向中国智造转型提供了生动范本。