在新能源客车产业高速发展的浪潮中,湖北星申动精密机械有限公司(以下简称"星申动")凭借其前瞻性的技术布局,正在书写一段关于制动鼓平衡技术的创新传奇,这家扎根于华中工业重镇的企业,在新能源客车核心部件的精密制造领域,用十年磨一剑的专注,构建起行业领先的工艺体系,其最新研发的第七代智能平衡系统,正为行业破解动能回收系统带来的平衡难题提供创新解决方案。
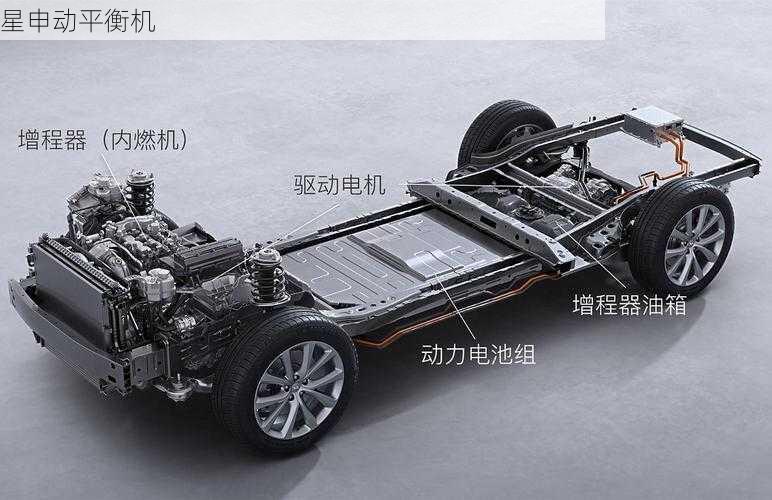
新能源变革催生平衡技术新标准
随着"双碳"战略的深入推进,我国新能源客车保有量以年均28%的增速持续攀升,与传统燃油车相比,新能源客车的动能回收系统带来了革命性的技术变革,当车辆制动时,驱动电机转换为发电机模式,将动能转化为电能储存,这一过程产生的逆向扭矩对制动系统造成持续冲击,使得制动鼓的受力模式发生根本性改变。
行业数据显示,搭载动能回收系统的新能源客车,其制动鼓平均承受的扭矩波动频率是传统车辆的3.7倍,动态平衡失效导致的异常磨损率高达传统车型的2.5倍,在此背景下,2023年实施的《新能源商用车制动系统技术规范》将制动鼓动平衡精度要求从G6.3级提升至G2.5级,这意味着允许的残余不平衡量缩减了60%以上。
动能回收系统的特殊平衡需求
星申动技术团队通过长期跟踪测试发现,动能回收系统对制动鼓平衡的影响主要体现在三个维度:首先是高频次的扭矩切换,单日运营中平均要经历2000次以上的能量转换;其次是动态载荷的复杂性,逆向扭矩与机械制动的叠加作用形成复合载荷谱;最后是热管理挑战,电能转化过程中产生的瞬时高温可达350℃,导致材料性能的阶段性改变。
这种特殊工况对平衡技术提出全新要求:传统静态平衡方案已无法满足需求,必须在动态工况下实现实时补偿;平衡配重的安装方式需要适应高频振动环境;检测系统要具备温度补偿和载荷谱分析能力,某头部客车企业曾做过对比试验,采用传统平衡方案的制动鼓在3万公里后出现0.15mm的偏磨,而符合新标准的制动鼓在同等工况下偏磨量控制在0.05mm以内。
星申动的技术创新路径
面对行业痛点,星申动构建了"三位一体"的技术攻关体系,在硬件层面,研发出具备多轴联动功能的动态平衡检测平台,通过六维力传感器实时采集制动鼓在模拟动能回收工况下的振动频谱,检测精度达到0.1g·mm级别,软件系统方面,开发了基于机器学习的智能补偿算法,能够根据载荷谱特征自动生成平衡修正方案,将调试效率提升40%以上。
材料工艺的创新同样关键,公司与华中科技大学材料学院联合研发的梯度复合涂层技术,通过在制动鼓关键部位沉积0.2mm的特殊合金层,将材料的热变形系数降低了35%,这项获得国家发明专利的技术(专利号:ZL2022103*****.X),使得制动鼓在温度剧烈变化时仍能保持优异的尺寸稳定性。
全生命周期解决方案的实践价值
在武汉某公交集团的实地应用中,装配星申动第七代平衡系统的120台纯电动公交车,创造了连续18个月零平衡失效的运营记录,其秘密在于创新的"动态平衡档案"系统:每个制动鼓在出厂时即建立数字孪生模型,通过车载传感器实时传回运行数据,当系统检测到平衡参数偏离阈值时,自动触发维护预警。
这种预防性维护模式使制动系统维护成本降低52%,单台车年均可节约运营成本1.2万元,更值得关注的是,星申动推出的再制造平衡服务,通过对退役制动鼓进行激光熔覆修复和动态平衡再造,使产品生命周期延长2-3倍,为运营商创造显著的循环经济效益。
标准引领与产业协同
作为全国汽车标准化技术委员会制动分标委成员单位,星申动深度参与了6项行业标准的制修订工作,其主导制定的《新能源客车制动鼓动态平衡试验方法》首次将动能回收工况纳入标准测试流程,填补了国内外技术标准空白,公司建设的国家级检测中心,已成为行业公认的平衡技术验证平台,年检测能力达5万件次。
在产业协同方面,星申动与国内TOP5客车制造商建立了联合实验室,针对不同车型开发定制化平衡方案,其最新研发的模块化平衡系统,可根据车辆配置自动调整参数,适配从8米社区巴士到18米铰接客车的全系车型,帮助整车企业缩短研发周期30%以上。
站在新能源客车产业转型升级的关键节点,星申动正以技术创新重新定义制动鼓平衡的标准体系,从精密制造到智能检测,从材料革新到服务升级,这家企业用持续的技术迭代证明:在汽车产业变革的宏大叙事中,核心零部件的突破往往源自对基础技术的极致追求,当越来越多的新能源客车搭载着"星申动方案"驰骋在城市道路上,我们看到的不仅是一家企业的成长轨迹,更是中国制造向高端攀升的生动注脚。