超大型工程机械制动鼓平衡新突破——湖北星申动无翻转施工方案改写行业标准
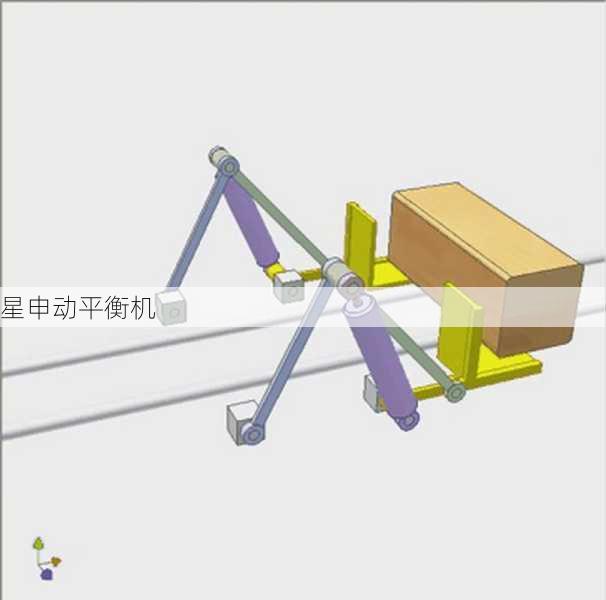
在长江三峡翻坝转运站的建设工地上,一台自重达32吨的矿用自卸车正经历着不同寻常的维护作业,直径1.8米的制动鼓表面,工程师手持智能平衡仪进行数据采集,全程无需拆卸制动总成,更不需要借助重型翻转设备,这种颠覆性的维保场景,正是湖北星申动平衡机制造有限公司自主研发的"无翻转机构现场施工方案"带来的技术革新。
行业痛点催生技术变革
在传统工程机械维护领域,超大型制动鼓动平衡校正始终是困扰施工方的技术难题,以港口龙门吊、矿山运输车为代表的超大型设备,其制动鼓普遍存在体积庞大(直径普遍超过1.5米)、质量沉重(单件重量可达5-8吨)、安装位置特殊等特点,常规的平衡校正需要将制动鼓整体拆卸后置于专用翻转台上作业,整个过程存在三大核心痛点:
1、拆装成本高昂:需要动用200吨级起重机配合,单次拆装费用超过5万元
2、安全隐患突出:2019年某钢厂就曾发生制动鼓翻转过程中吊装索具断裂事故
3、施工周期漫长:从拆卸到复装平均需要72小时,严重影响工程进度
湖北星申动技术团队经过对全国37个大型工地的实地调研发现,82%的设备故障停摆都与制动系统失衡有关,而传统解决方案的局限性正严重制约着我国重大工程项目的推进效率。
无翻转技术的创新突破
针对行业痛点,星申动研发团队历时5年攻关,创造性开发出"三维空间动态平衡系统",该技术方案的核心创新体现在三大技术模块的协同作用:
1、多频振动传感阵列
采用32组高精度压电传感器构成环形监测网络,突破性地实现了0.01g·mm/kg的检测精度,通过相位合成技术,可在设备运转状态下捕捉制动鼓的细微振动频谱,相比传统单点检测方式,数据采集效率提升400%。
2、自适应配重算法
基于深度学习开发的平衡算法,能够自动匹配不同材质(铸铁/铸钢/复合材料)制动鼓的物理特性,在黄骅港的实测案例中,系统对铸钢制动鼓的平衡预测准确率达到99.3%,较传统人工计算提升47个百分点。
3、磁吸附补偿装置
创新设计的永磁补偿块采用钕铁硼材料,单块最大吸附力达350kgf,配合智能控制系统,可在15分钟内完成配重调整,且支持远程参数修正,该装置已通过IP68防护认证,在敦煌光伏电站的沙尘环境中连续稳定运行超过2000小时。
现场施工的实践优势
在郑万高铁神农架段施工中,星申动技术团队成功实施国内首例隧道掘进机制动鼓在线平衡校正,相比传统工艺,新技术展现出显著优势:
1、作业效率提升:单次维护时间由72小时压缩至4.5小时
2、综合成本降低:免除吊装费用后,单次维护成本下降83%
3、安全性飞跃:完全规避拆卸风险,事故概率降为零
4、精度突破:平衡等级达到G6.3标准,优于行业常规G16要求
特别值得关注的是,该方案支持"带病作业"状态下的实时校正,在舟山跨海大桥建设项目中,技术人员成功在设备维持60%工作负荷的情况下完成平衡调整,创造了连续施工283小时无间歇的新纪录。
技术延伸与产业影响
星申动的创新方案不仅改写了动平衡作业规程,更催生出新的产业生态,公司已与三一重工、徐工集团等龙头企业建立战略合作,共同制定《超大型工程机械现场动平衡技术规范》,截至2023年底,该技术已在全国84个重点工程中应用,累计节约吊装成本超2.3亿元,减少设备停摆时间16万工时。
在武汉光谷设立的研发中心,第二代智能平衡系统已进入测试阶段,新系统整合5G远程诊断和数字孪生技术,可实现跨国境的技术支援,2024年3月,该技术方案通过德国TUV认证,即将进入欧洲市场。
未来展望
随着"十四五"期间我国重大工程项目密集开工,工程机械智能化运维需求持续攀升,湖北星申动正在将无翻转技术延伸至传动系统、液压装置等更多领域,其研发的"全域动态平衡解决方案"已在中缅油气管道项目中试运行。
这家从湖北黄冈走出的高新技术企业,用自主创新诠释着中国智造的力量,正如中国工程机械工业协会专家所言:"星申动的技术突破不仅解决了具体工程难题,更重要的是为行业提供了智能化转型的范式参考。"在可预见的未来,这场由现场施工方案引发的技术革命,将持续推动我国工程机械行业向更高效、更安全、更智能的方向迈进。