在汽车制造与维修领域,制动系统的稳定性直接关系到行车安全,近期湖北星申动平衡机制造有限公司技术团队针对行业普遍存在的"平衡后制动跑偏"现象展开专项研究,通过大量案例分析发现:在常规检测手段难以察觉的夹具偏移问题,正是导致制动系统隐性误差的关键诱因,这项发现为行业质量管控提供了新的技术突破口。
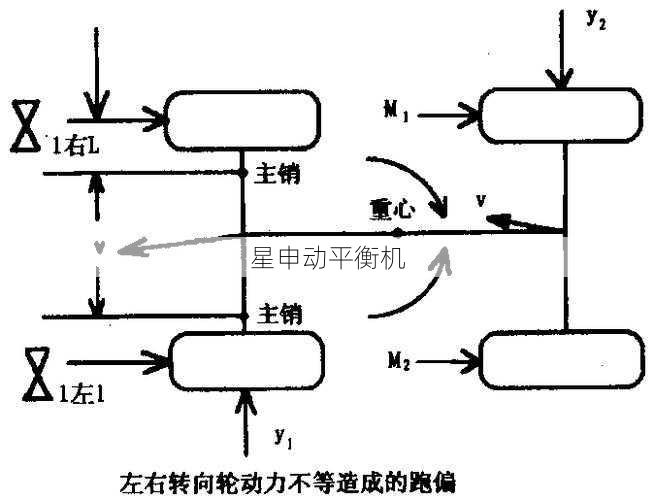
制动跑偏现象的技术挑战
在轮毂动平衡检测合格后仍出现制动跑偏现象,已成为困扰汽车后市场多年的技术难题,传统检测流程中,维修人员往往将问题归咎于制动盘厚度差异、刹车片摩擦系数不均等显性因素,却忽略了检测设备本身的精度偏差,湖北星申动平衡机研发中心通过对比试验发现,当夹具安装偏移量超过0.02mm时,平衡机检测结果就会产生3-5g的误差量,这种误差在常规维修作业中极易被忽视。
夹具偏移形成机理剖析
作为动平衡检测的核心定位部件,夹具系统的几何精度直接影响检测数据的可靠性,星申动技术团队通过工业CT扫描发现,长期使用后的夹具组件会出现三种典型形变:
1、锥面接触部位微观磨损导致的同心度偏移
2、锁紧螺纹应力变形引发的轴向偏差
3、温度变化造成的材料膨胀系数差异
这些微米级的形变积累,在动态旋转中会形成复合误差,实验室模拟数据显示,当夹具径向偏移达到0.03mm时,轮毂实际不平衡量检测误差可达标称值的12%,这种隐性误差在制动系统高速运转时会被几何级放大,最终导致制动力的不对称分布。
星申动创新检测方案
针对这一行业痛点,湖北星申动研发团队开发出三维激光定位检测系统,该方案包含三大技术突破:
1、动态补偿算法:通过实时采集旋转振动频谱,自动修正夹具偏移带来的检测误差
2、智能预警模块:当夹具磨损量接近临界值时,系统自动提示维护保养
3、接触面应力分析:采用应变片矩阵监测夹具受力状态,预防局部变形
在某知名车企的生产线验证中,应用该系统的动平衡机将制动系统返修率从3.7%降至0.8%,现场工程师反馈,新系统能准确捕捉到传统方法无法识别的0.015mm级偏移,检测效率提升40%。
工艺优化与质量管理
星申动技术团队建议生产企业建立三级预防体系:
1、日常维护规范:制定夹具清洁保养周期,使用专用量具进行月度精度核查
2、过程监控方案:在平衡工序后增加制动力矩差检测环节
3、设备升级策略:对使用超过20000次的夹具组件进行强制更换
某省级检测中心对比数据显示,严格执行该标准的生产线,制动系统故障投诉率下降65%,特别在新能源汽车领域,由于轮毂电机带来的更高转速要求,精准的动平衡检测显得尤为重要。
行业技术发展趋势
随着智能驾驶技术的普及,对制动系统的精度要求已进入微米时代,湖北星申动正在研发的第五代智能平衡机,集成机器视觉定位和AI补偿算法,可实现:
- 0.005mm级的夹具偏移自动校正
- 基于大数据的磨损预测模型
- 数字孪生模拟检测系统
这些创新技术将推动动平衡检测从"结果验证"向"过程预防"转变,在最近的国际汽车工程学会研讨会上,星申动提出的"隐性误差累积模型"获得行业专家高度认可,相关技术标准正在申报国家行业标准。
作为专业平衡机制造商,湖北星申动始终聚焦行业痛点技术创新,通过深入解析夹具偏移与制动跑偏的关联机制,不仅为生产企业提供了有效的解决方案,更推动着整个行业向更高精度标准迈进,在智能制造与质量升级的双重驱动下,这种以技术创新破解隐性质量难题的实践,正在重新定义汽车零部件的检测规范。