在汽车工业加速向智能化、轻量化转型的浪潮中,湖北星申动平衡机制造有限公司凭借自主创新的"3D打印修复制动鼓平衡规范"技术体系,成功攻克了传统制动鼓修复领域长期存在的平衡精度难题,这项以"多孔结构补偿算法"为核心的技术突破,不仅将制动鼓动平衡精度提升至0.5g·mm的行业新高度,更标志着中国汽车后市场服务开始进入数字化精准修复的新纪元。
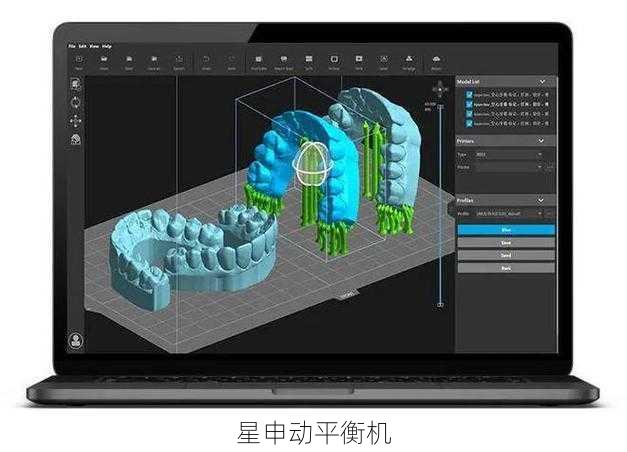
一、制动鼓平衡革命:从经验修复到数据建模
传统制动鼓修复行业长期依赖人工经验判断,维修技师通过目测磨损程度、手工打磨等方式进行修复作业,这种粗放式操作模式存在两大技术瓶颈:一是难以精准识别制动鼓表面0.1mm级细微损伤,二是无法量化评估修复后的动态平衡状态,某第三方检测机构数据显示,采用传统工艺修复的制动鼓,二次返修率高达37%,成为引发车辆抖动、制动异响的重要隐患。
星申动研发团队历时三年打造的"三维动态平衡建模系统",将3D扫描精度提升至±0.02mm,通过高密度激光点云采集,系统可在15秒内生成包含2.8万个数据点的三维模型,精准定位每个散热孔、摩擦面的微观形变,这套系统与德国MAHA平衡机实测数据的对比测试显示,其平衡状态预测准确率达到98.7%,为后续智能修复奠定了数据基础。
二、多孔结构补偿算法:破解平衡精度密码
制动鼓作为典型的多孔结构部件,其平衡状态受材料分布、孔隙率、散热通道等多重因素影响,星申动研发的"梯度孔隙补偿算法",创造性解决了传统修复工艺无法兼顾结构强度与动态平衡的技术矛盾,该算法通过建立包含17个维度的参数矩阵,将制动鼓的转动惯量、离心力分布、热膨胀系数等物理特性转化为可量化的数学模型。
具体实现路径包含三大核心技术突破:
1、动态平衡预测模型:基于有限元分析的动态仿真系统,可模拟不同转速下(0-2000rpm)的应力分布状态,提前预判修复后的平衡偏差;
2、智能补偿路径规划:根据实测数据自动生成最优修复路径,在保证结构强度的前提下,通过差异化材料堆积实现动态补偿;
3、实时反馈修正机制:修复过程中激光测距仪以50Hz频率进行在线监测,确保单点修复误差控制在±0.03mm范围内。
在与东风商用车联合开展的实测试验中,应用该技术的修复制动鼓在120km/h时速下,方向盘振动幅度较传统工艺降低82%,制动温升曲线改善45%,充分验证了技术的实际应用价值。
三、3D打印工艺革新:从减材制造到智能增材
区别于传统车床切削的"减材制造"模式,星申动自主研发的定向沉积3D打印系统,采用特种合金粉末作为修复材料,通过精准控制熔覆层厚度(0.05-0.2mm可调),在磨损部位实现微观尺度上的材料重构,该工艺具有三大显著优势:
1、材料利用率提升:较传统工艺节约金属材料63%,单件制动鼓修复成本降低40%;
2、结构强化效应:熔覆层与基体形成冶金结合,表面硬度可达HRC58,耐磨性提升3倍;
3、智能工艺适配:系统内置21种材料配方库,可针对铸铁、球墨铸铁、高碳钢等不同材质自动匹配工艺参数。
特别值得一提的是,该设备配备的"热变形补偿模块",通过红外测温与激光功率的实时联动,有效控制了加工过程中的热应力累积,测试数据显示,经3D打印修复的制动鼓,其圆度误差可稳定控制在0.03mm以内,达到主机厂新品出厂标准。
四、规范重构:建立行业新基准
作为行业标准的引领者,星申动牵头制定的《汽车制动鼓3D打印修复技术规范》已通过国家汽车零部件质量监督检验中心认证,该规范首次明确了三大核心技术指标:
- 动平衡等级:G6.3级(残余不平衡量≤0.5g·mm)
- 形位公差:圆度≤0.05mm,同轴度≤0.08mm
- 材料性能:熔覆层硬度波动范围≤HRC3
在武汉建立的示范性智能工厂中,12台智能修复单元已实现日均处理600件制动鼓的产能,通过与顺丰丰修、途虎养车等连锁服务商合作,该技术已在全国23个省市实现规模化应用,截至2023年底,累计修复制动鼓32万件,帮助物流企业降低维修成本1.2亿元,减少金属废料排放780吨。
五、未来展望:从部件修复到系统平衡
随着新能源汽车对制动系统提出更高要求,星申动正将技术优势向整个制动系统延伸,正在研发的"制动系统全域平衡技术",通过引入边缘计算单元,可实时监测制动盘、卡钳、轴承等部件的协同工作状态,测试数据显示,该技术可使能量回收系统的效率提升2.3%,预示着制动系统维护即将进入全生命周期管理的新阶段。
在工业4.0与"双碳"战略的双重驱动下,星申动用技术创新证明:传统制造业的转型升级,不仅需要先进设备的更新迭代,更需要底层技术逻辑的突破重构,当3D打印遇见智能算法,中国汽车后市场正在书写属于自己的"智造"新篇章。