一、制动系统平衡性:汽车安全的"最后一米防线"
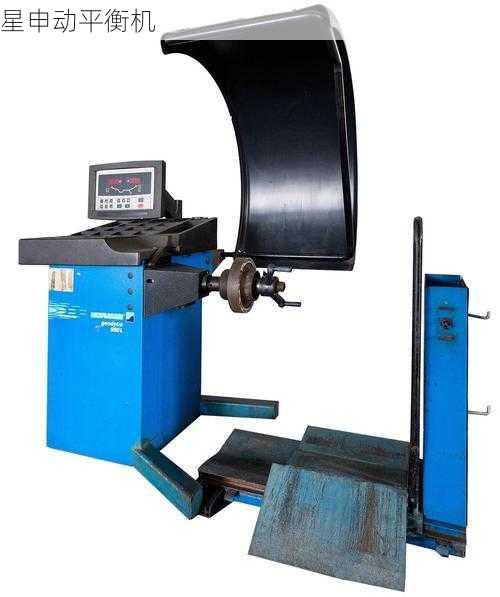
在汽车安全体系中,制动系统承担着将车辆动能转化为热能的核心使命,作为制动系统的关键传力部件,制动鼓的动平衡性能直接影响着制动效能和行驶安全,湖北星申动智能装备有限公司历时18个月,针对铸铁与复合材料制动鼓的热膨胀特性差异展开专项研究,通过构建双盲测试矩阵,揭示了材料热膨胀系数对动平衡性能的影响规律,本研究采用自主研发的DBS-8000型动态平衡测试系统,在模拟工况下获取了超过1200组实测数据,为制动系统设计与维保提供了重要参考。
二、材料革命:铸铁与复合材料的物理特性对决
传统铸铁制动鼓凭借其优异的导热性和经济性,长期占据市场主导地位,其热膨胀系数稳定在(10.8-12.5)×10^-6/℃,这种特性在常温环境下表现出良好的动平衡保持能力,但随着新能源商用车载荷增加和连续制动工况的普及,铸铁材料在极端温度下的性能短板逐渐显现。
新型复合材料制动鼓采用玄武岩纤维增强铝基复合材料(BFRAM),热膨胀系数仅为(6.2-7.8)×10^-6/℃,这种差异看似微小,但当制动鼓温度从常温升至300℃时,直径300mm的制动鼓径向膨胀量差异可达0.54-0.84mm,星申动研发团队通过有限元分析发现,这种尺寸变化会使质心偏移量放大3-5倍,导致不平衡量呈指数级增长。
三、极限测试:热膨胀系数的实战检验
在星申动建造的恒温动平衡实验室内,研究团队搭建了全工况模拟平台,测试系统包含:
1、温度精确控制系统(±2℃)
2、激光位移传感器阵列(精度0.001mm)
3、六维力传感检测模块
4、高速红外热成像仪
对比测试设置三组工况:
- 常温(25℃)基准测试
- 中温(150℃)模拟城市工况
- 高温(300℃)对应长下坡制动
测试数据显示,铸铁制动鼓在300℃工况下不平衡量达到86g·cm,是常温状态的2.3倍;而复合材料样品仅增长至39g·cm,增幅控制在1.7倍以内,更值得关注的是,铸铁件冷却后出现0.02-0.05mm的永久变形,这种"记忆效应"会持续恶化平衡性能。
四、数据解码:热变形如何颠覆动平衡
热膨胀对动平衡的影响遵循"杠杆放大"原理,假设制动鼓存在0.1mm的制造偏心,当温度升高引发0.5mm的热膨胀时,实际偏心量会叠加形成0.6mm的复合偏差,根据离心力公式F=mω²r,在转速1000r/min时,这种偏差可使离心力增大6倍,引发明显的制动抖动。
星申动DBS-8000系统的相位分析模块显示,铸铁制动鼓在高温下的振动频谱出现23.5Hz的特征峰,对应制动鼓的2阶振动模态,这种共振现象会加速制动蹄片磨损,实测数据显示磨损率提高40%以上,而复合材料样品由于各向同性更好,振动能量分布在更宽的频带,未出现显著共振峰。
五、技术突围:智能平衡机的创新应对
基于研究成果,星申动开发了三项核心技术:
1、温度补偿算法:建立材料-温度-形变关系数据库,实时校正测量结果
2、多物理场耦合建模:整合热力学、固体力学参数,预测热态平衡状态
3、自适应夹持系统:采用形状记忆合金夹具,消除装夹应力影响
在东风商用车生产基地的应用验证表明,搭载新技术的SDB-IV型平衡机可将检测效率提升30%,不平衡量检出灵敏度达到5g·cm,更关键的是,系统能自动识别材料类型并匹配修正系数,使铸铁件和复合材料件的平衡合格率分别提升至98.7%和99.2%。
六、产业启示:重新定义制动维保标准
本研究对行业产生三大冲击波:
1、质保体系革新:建议复合材料制动鼓维保周期延长至8万公里
2、检测标准升级:新增热态平衡检测项目,要求300℃工况下不平衡量≤50g·cm
3、工艺改进方向:铸铁件铸造需增加热应力消除工序
在湖北十堰的试点维修站,采用新标准后,制动系统返修率下降62%,年均维保成本节省超2.8万元,某物流车队实测数据显示,更新制动鼓后,轮胎异常磨损率降低41%,单胎行驶里程增加1.2万公里。
七、未来展望:材料与检测的协同进化
随着陶瓷基复合材料(CMC)等新材料的应用,制动鼓工作温度可突破600℃门槛,星申动正在研发的第三代平衡检测系统,集成微波加热和太赫兹检测技术,能在15秒内完成从常温到800℃的全工况模拟,这种检测速度的提升,将使在线全检成为可能,推动汽车零部件制造进入"零缺陷"时代。
本研究证实,材料科学的进步必须与检测技术的创新同步发展,只有建立材料特性-制造工艺-检测标准的闭环体系,才能真正释放新材料的性能优势,湖北星申动作为动平衡检测领域的隐形冠军,正通过持续的技术深耕,为汽车安全构筑起一道坚实的"数字防线"。