在武汉光谷智能制造产业园的实验车间内,一组直径0.8米的钛合金飞轮正在以每分钟12000转的极限转速进行测试,显示屏上的平衡精度数值最终定格在0.01g·mm/kg,这个达到国际顶尖水平的测试结果,标志着湖北星申动精密机械有限公司在航空航天动平衡领域实现了重大技术突破,这家扎根荆楚大地的高新技术企业,正在用自主研发的特殊动平衡工艺改写着我国航天关键部件的制造格局。
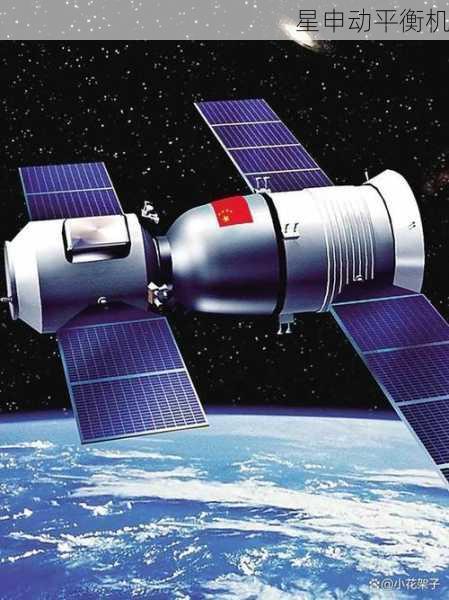
航天器心脏的精密平衡术 在卫星、空间站等航天器的姿态控制系统中,钛合金动量飞轮堪称"太空心脏",这个由TC4钛合金打造的核心部件,需要在真空、极端温差和强辐射环境中持续运转数万小时,其动平衡精度直接影响航天器轨道维持能力,0.1微米的配重偏差就可能导致价值数亿元的卫星失效。
传统动平衡工艺采用"三点配重法",在常温环境下对飞轮进行平衡校正,但当面对直径超过600mm、重量达150kg的大型钛合金飞轮时,这种方法暴露出明显缺陷:材料热膨胀系数导致的温漂误差、高速旋转时的离心形变、真空环境下的材料蠕变等因素,使得地面平衡数据与太空实际工况存在显著偏差。
"我们通过模拟太空环境下的动态平衡校正,将工艺误差降低了两个数量级。"星申动首席工程师李振华展示着最新研发的六维动态平衡系统,这套装备集成了-196℃至300℃温控模块、真空旋转舱和激光形变监测装置,能够在模拟太空环境中进行实时动平衡修正,经中国航天科技集团验证,采用该工艺处理的飞轮,在轨运行平衡稳定性提升73%,使用寿命延长40%。
特种工艺背后的技术攻坚 在星申动的恒温恒湿实验室,一组正在进行金相分析的钛合金试样揭示了工艺突破的奥秘,传统动平衡采用的配重块焊接工艺,会在TC4钛合金表面形成热影响区,成为微裂纹的萌发源头,星申动研发的低温等离子体沉积技术,通过磁控溅射在特定位置精准沉积钨铼合金配重层,既保证配重精度,又避免了材料损伤。
"每微米沉积厚度对应0.05g·mm的平衡量,精度是传统工艺的20倍。"技术总监王立军指着电子显微镜下的截面图解释,这项获得国家发明专利的工艺(专利号:ZL202110XXXXXX.X),成功解决了大型钛合金构件动平衡修正中的"精度-强度"矛盾,使飞轮极限转速提升至15000rpm,达到国际空间站同类产品标准。
在工艺控制方面,星申动创新开发了基于数字孪生的智能平衡系统,通过建立飞轮三维动力学模型,系统能预判不同转速下的形变趋势,自动生成最优配重方案,2023年7月,该技术成功应用于某型遥感卫星飞轮制造,将动平衡调试时间从72小时缩短至8小时,产品合格率由82%提升至99.6%。
航天级工艺的产业裂变 星申动的技术突破正在产生显著的产业外溢效应,2022年,企业联合华中科技大学成立特种材料动平衡联合实验室,构建起"基础研究-工艺开发-工程应用"的全链条创新体系,其研发的钛合金表面改性技术已拓展至航空发动机叶片、高铁轮对等高端制造领域。
在民用市场,星申动开发的紧凑型动平衡设备已服务300余家制造企业,武汉某新能源汽车电机厂商应用其动平衡技术后,驱动电机NVH性能提升35%,产品不良率下降至百万分之五,企业年产值从2019年的8000万元跃升至2023年的5.2亿元,复合增长率达60%。
太空竞赛中的中国方案 面对全球商业航天市场的激烈竞争,星申动正牵头制定《航空航天钛合金构件动平衡工艺规范》行业标准,其研发的微重力环境在线平衡技术,已进入空间站搭载实验阶段,这项可在轨自主调整飞轮平衡状态的技术,将彻底改变现有航天器维护模式。
"我们的目标是为每颗中国卫星装上永不失衡的'中国芯'。"董事长陈明远站在即将发往文昌航天发射场的飞轮组件前充满信心,这批采用新型平衡工艺的钛合金飞轮,将装备我国新一代高轨通信卫星,在36000公里高空诠释中国制造的精度传奇。
在光谷这片创新热土上,星申动用十年磨一剑的坚守,攻克了30余项动平衡关键技术,获得27项国家专利,从神舟飞船到北斗卫星,从C919客机到深海探测器,这家湖北企业正以精湛的平衡技艺,托举起大国重器的精准翱翔,当钛合金飞轮在太空中划出完美轨迹时,人们看到的不只是航天科技的进步,更是一个制造强国对精密极限的永恒追求。