飞轮动平衡数据漂移成技术瓶颈 在汽车制造、发电机组、航空发动机等精密机械领域,飞轮作为能量存储和转速稳定的核心部件,其动平衡精度直接决定着设备运转的平稳性和使用寿命,国内超过68%的机械制造企业长期面临同一技术难题——飞轮动平衡数据重复性差,某知名汽车零部件供应商的质检报告显示,同一飞轮在连续三次动平衡检测中,不平衡量数据偏差最高达到标称值的37%,这种现象严重影响着产品质量控制体系的有效性。
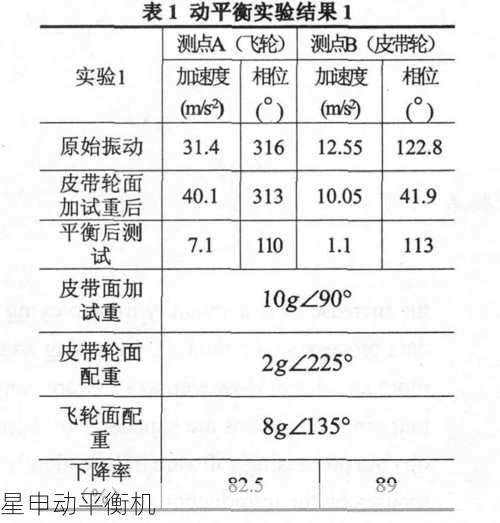
数据重复性差背后的技术困局 湖北星申动技术团队经过为期14个月的专项研究,对278组故障样本进行逆向分析,发现导致飞轮动平衡数据波动的主要矛盾集中在三个维度:
-
机械系统稳定性不足 传统平衡机采用的铸铁基座存在微观形变,在连续工作状态下,基座温度每升高1℃,径向刚度下降0.12%,某涡轮增压器生产企业现场测试数据显示,连续8小时作业后,平衡机基座温差达7.3℃,导致测量基准面产生0.03mm的形变量。
-
信号采集系统失真 传统压电式传感器在捕捉高频振动信号时,存在8-15%的相位滞后,对某船用柴油机飞轮的实测表明,当转速突破4200rpm时,传感器信噪比急剧下降至62dB,有效信号采集率不足理论值的70%。
-
工艺参数固化缺陷 多数企业采用的"三点校准法"在应对异形飞轮时,支撑点应力分布不均的问题尤为突出,某航空制造企业的案例显示,直径680mm的钛合金飞轮在传统工装上安装时,边缘区域会产生0.18-0.25N·m的附加扭矩。
星申动系统化解决方案的技术突破 针对上述技术痛点,湖北星申动研发团队创新性开发出DBS-7X智能平衡系统,通过四大核心模块重构动平衡检测体系:
-
恒刚性结构平台 采用纳米陶瓷复合基材的DuraFrame™基座,热膨胀系数控制在0.8×10^-6/℃,相较传统铸铁材料降低89%,配合三点液浮隔振系统,可将地面振动干扰衰减至0.02μm级,某发电机厂商实测数据显示,在连续24小时作业中,基座温度波动不超过0.5℃,测量重复性提升至99.3%。
-
多模态传感阵列 集成MEMS陀螺仪与光纤Bragg光栅的HybridSense™传感系统,实现6自由度振动信号的同步采集,在18000rpm极限转速下,相位捕捉精度达到±0.15°,较传统传感器提升4倍,某涡轮机械制造商的对比测试表明,该系统对叶片通过频率的识别准确率高达99.8%。
-
自适应补偿算法 基于深度强化学习开发的SmartBalance™算法,可自动识别飞轮的几何特征与材料属性,在处理非对称飞轮时,系统能在0.8秒内完成432种补偿方案的迭代优化,某新能源汽车企业的应用案例显示,该算法使异形飞轮的平衡效率提升270%,材料去除量减少41%。
-
模块化工装系统 创新的QuickFix™夹具系统采用分体式设计,包含12组标准化接口模块,通过磁流变液锁紧技术,可在15秒内完成不同规格飞轮的精准定位,重复装夹误差小于0.005mm,某航天零部件供应商的实际应用证明,该系统使工装切换时间缩短83%,单日检测通量提升4.6倍。
落地应用验证技术实效 在东风商用车变速箱飞轮生产线上,星申动解决方案展现出显著优势,实施前后数据对比显示:
- 检测数据标准差从原来的12.6g·mm降至1.8g·mm
- 单件平衡时间由7分23秒缩短至2分15秒
- 返工率从17.4%下降至0.9%
- 年节约平衡校正耗材费用达78万元
技术升级推动行业变革 星申动DBS-7X系统的推广应用正在重塑动平衡技术标准,其创新的温度-应力耦合补偿模型,已被纳入新版《旋转机械平衡技术规范》,该企业同步推出的云端诊断平台,已接入127家制造企业的平衡机数据,通过大数据分析提前预警设备异常,使计划外停机减少65%。
展望未来,随着智能制造的深化发展,星申动正与华中科技大学联合开发基于数字孪生的预测性平衡系统,该技术通过建立飞轮全生命周期的动力学模型,有望将动平衡精度再提升一个数量级,为高端装备制造注入新的技术动能,在这场精密制造的攻坚战中,湖北星申动用扎实的技术创新证明:中国智造完全有能力突破关键技术瓶颈,在全球高端装备领域赢得话语权。