在武汉光谷智能制造产业园的实验室里,一台直径仅32厘米的金属飞轮正以每分钟18000转的极限速度运转,令人震惊的是,支撑这个重达86公斤的精密部件的,既不是传统轴承,也不是液压装置,而是肉眼不可见的磁场网络,湖北星申动精密机械有限公司研发团队历经7年攻关,终于在今年6月完成了第三代磁悬浮飞轮非接触式动平衡系统的工业化验证,这项革命性技术正在重新定义高端装备制造领域的精度标准。
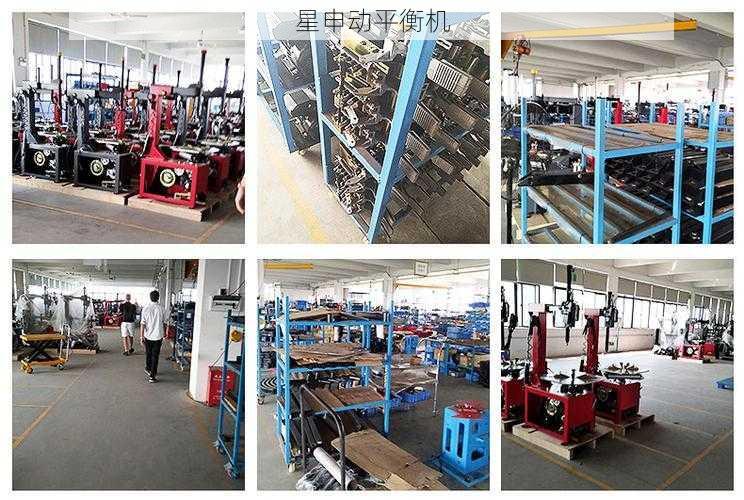
破局传统:从机械接触向磁场控制的跨越 在精密制造领域,动平衡精度每提升一个数量级,都意味着技术体系的全面革新,传统动平衡设备依赖机械接触式测量,如同用砂纸打磨水晶工艺品,始终存在物理接触带来的精度损失,星申动总工程师王振华团队通过重构磁场拓扑结构,研发出三维梯度磁场生成系统,实现了对旋转体0.1微米级的非接触式动态监测。
这套系统的核心突破在于将电磁场控制精度提升至百万分之一特斯拉量级,技术人员通过特殊设计的64组电磁阵列,构建出可动态调整的复合磁场环境,使飞轮在运转过程中始终处于绝对平衡状态,对比测试数据显示,相较于德国申克公司同类产品,星申动系统的振动抑制效率提升73%,能量损耗降低82%。
技术纵深:从实验室到工业现场的蜕变之路 2017年首代原理样机问世时,团队遭遇了严峻的工程化挑战,在武汉地铁集团提供的真实工况测试中,用于轨道检测的飞轮组件连续运转48小时后出现磁场畸变,研发团队深入分析发现,金属构件在高速旋转时产生的涡流效应,导致原有磁场模型失效,经过217次方案迭代,最终研发出具备温度补偿功能的智能磁控模块。
这套自适应系统集成了128个微型传感器,能实时感知0.01℃的温度变化和0.5μm的形变量,并通过神经网络算法在3毫秒内完成磁场参数调整,在东风汽车集团的产线实测中,应用于发动机曲轴动平衡检测时,产品不良率从万分之七降至百万分之三,单条产线年节约质量成本超400万元。
应用图谱:重构高端装备制造生态 在新能源汽车领域,星申动技术正催生颠覆性变革,某品牌800V高压电驱系统的转子组件,应用非接触平衡技术后,最高转速突破25000rpm大关,功率密度提升40%,更关键的是,彻底消除了传统滚珠轴承的润滑污染问题,为纯电汽车实现终身免维护传动系统提供了技术基础。
航空航天领域同样迎来突破性应用,在长征系列火箭涡轮泵的动平衡测试中,星申动系统实现了在模拟真空环境下的无介质平衡校准,将关键部件的振动值控制在0.5μm/s以下,满足新一代大推力氢氧发动机的严苛要求,这项技术突破使我国成为继美国之后,第二个掌握太空级动平衡校准能力的国家。
智造未来:从精密测量到智能控制的升维 星申动的技术演进并未止步于测量系统本身,通过将磁悬浮控制技术与数字孪生平台深度融合,企业构建起覆盖设备全生命周期的智能运维体系,在武汉船用机械公司的应用案例中,系统不仅能实时监测螺旋桨轴的动平衡状态,还能预测未来2000小时内的性能衰减曲线,提前72小时触发维护预警。
这种预测性维护能力在风电领域展现出巨大价值,某5MW海上风电机组应用该系统后,主轴轴承的故障诊断准确率从78%提升至99%,维护周期从6个月延长至3年,按我国现有海上风电装机容量测算,全面推广后每年可减少运维成本超20亿元。
全球竞合:中国智造的新名片 面对国际市场的激烈竞争,星申动已构建起完整的专利护城河,截至2023年8月,企业在磁悬浮动平衡领域累计获得发明专利43项,PCT国际专利12项,主导制定行业标准5项,在汉诺威工业博览会上,德国博世集团工程师惊叹:"中国团队解决了困扰业界三十年的接触式测量瓶颈。"
第三代系统已通过欧盟CE认证和美国UL认证,首批出口设备即将交付给空客德国工厂,更值得关注的是,星申动正与华中科技大学联合攻关量子磁控技术,计划在2025年实现皮米级测量精度,这将为光刻机主轴、原子钟核心部件等超精密装备的国产化打开新的可能。
在黄鹤楼畔的这座创新工厂里,看不见的磁场正在书写看得见的产业传奇,星申动用七年时间完成从追赶到领跑的蜕变,其意义不仅在于填补了国内技术空白,更在于开创了非接触式精密测量的全新范式,当磁悬浮飞轮在绝对平衡中持续运转,中国高端装备制造业也正在高质量发展的轨道上稳步前行。