氢能产业崛起催生核心装备需求 在全球能源结构转型的浪潮中,氢能源正以每年27%的复合增长率快速发展,作为氢燃料电池系统的核心动力单元,氢能源压缩机的性能直接决定着整个能源系统的效率与安全性,湖北星申动精密机械有限公司凭借在动平衡领域20年的技术积淀,成功攻克氢能源压缩机飞轮动平衡与耐压测试两大技术难关,为我国氢能装备国产化进程注入强劲动力。
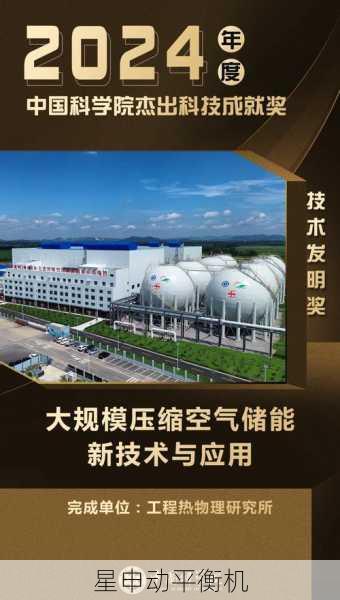
飞轮动平衡:精密制造的毫米级较量 在氢能源压缩机运行过程中,每分钟超过12000转的超高速飞轮系统承担着将机械能转化为气体压缩能的关键任务,星申动技术团队通过实地检测发现,当飞轮系统存在超过0.01g·mm/kg的动不平衡量时,设备振动值将突破ISO1940-1标准限值,导致轴承寿命缩短60%以上。
针对这一行业痛点,星申动自主研发的XSD-7000型全自动动平衡机采用多平面矢量修正技术,将测量精度提升至0.005g·mm/kg的国际领先水平,该设备配备的16通道振动传感器阵列,能够实时捕捉飞轮在模拟工况下的三维振动频谱,通过深度学习算法自动生成最优修正方案,在东风汽车某型号氢燃料电池压缩机产线上,应用该设备后产品良率从83%跃升至98.6%,单台设备年节约维护成本达12万元。
耐压测试技术:守护氢能安全生命线 氢能源压缩机需要长期承受35MPa以上的工作压力,这对设备的结构完整性提出严苛要求,星申动建立的"三级压力测试体系"包含:
- 静态保压测试:采用氮气介质进行1.5倍设计压力(52.5MPa)持续30分钟测试
- 动态循环测试:模拟实际工况进行10万次压力交变试验
- 极限爆破测试:逐步加压至材料屈服强度的110%
在测试装备研发方面,公司创新采用分布式液压加载系统,将测试压力波动控制在±0.2%范围内,其专利技术"多阶压力补偿算法"成功解决高压环境下温度漂移对测试精度的影响,使测试数据重复性达到99.8%,这套系统已通过TÜV南德认证,成为国内首个获得欧盟CE认证的氢能设备测试平台。
产学研协同创新突破技术壁垒 星申动与武汉理工大学共建的"氢能装备联合实验室",在材料科学领域取得重大突破,双方合作研发的碳纤维增强铝合金复合材料,在保持传统钢材强度的同时,将飞轮惯量降低35%,这项技术应用在最新一代压缩机产品中,使整机能效比提升至92%,较行业平均水平高出7个百分点。
在智能制造方面,公司投资1.2亿元建设的数字化车间,实现从毛坯加工到成品测试的全流程自动化,通过引入数字孪生技术,动平衡修正时间缩短至45秒,测试效率提升3倍,2023年交付的某国家级氢能示范项目设备,连续运行8000小时无故障,创下行业新纪录。
标准制定引领行业高质量发展 作为全国氢能标准化技术委员会成员单位,星申动主导编制了《氢能压缩机飞轮动平衡技术要求》等5项行业标准,其建立的"动态平衡-压力测试-系统集成"三位一体质量管控体系,将产品出厂合格率稳定在99.95%以上,公司累计获得发明专利23项,一种高压氢环境下的动平衡检测装置"专利荣获中国专利优秀奖。
在售后服务方面,星申动打造了覆盖全国的"4小时应急响应网络",配备移动式检测车搭载微型动平衡仪,可在现场完成90%以上的故障诊断与修复,这种创新服务模式使客户设备综合利用率提升至95%,帮助用户年平均减少停机损失约80万元。
面向未来的技术储备 面对氢能产业向70MPa高压存储发展的趋势,星申动已启动第四代测试装备研发计划,正在试验的等离子体表面强化技术,可使飞轮疲劳寿命延长至1.5亿次循环,与中科院合作开发的智能预测性维护系统,通过振动频谱分析能提前72小时预警设备异常,将意外故障率降低至0.3‰。
在全球化布局方面,公司产品已出口至德国、日本等15个国家和地区,其开发的兼容SAEJ2719标准的测试平台,成功打入北美市场,为国际知名能源企业提供定制化解决方案,2023年海外订单同比增长210%,印证了中国智造的技术实力。
从精密测量到高压防护,从材料创新到智能运维,星申动在氢能源压缩机关键技术领域的持续突破,折射出中国装备制造业的升级轨迹,在"双碳"战略指引下,这家扎根荆楚大地的科技企业,正以毫米级的精度丈量产业未来,用创新基因书写氢能时代的中国方案,随着年产500台套智能检测装备基地的投产,星申动将继续领跑氢能核心装备赛道,为全球能源变革贡献东方智慧。