在工业制造领域,动力系统的稳定性直接影响着生产效率和设备寿命,作为旋转机械核心部件的飞轮,其动平衡精度每提升1μm,就能减少3%的非计划停机风险,湖北星申动平衡机制造有限公司凭借二十年专业积淀,推出的新一代智能飞轮动平衡机,正以独特的全周期成本管理理念,重新定义行业运维标准。
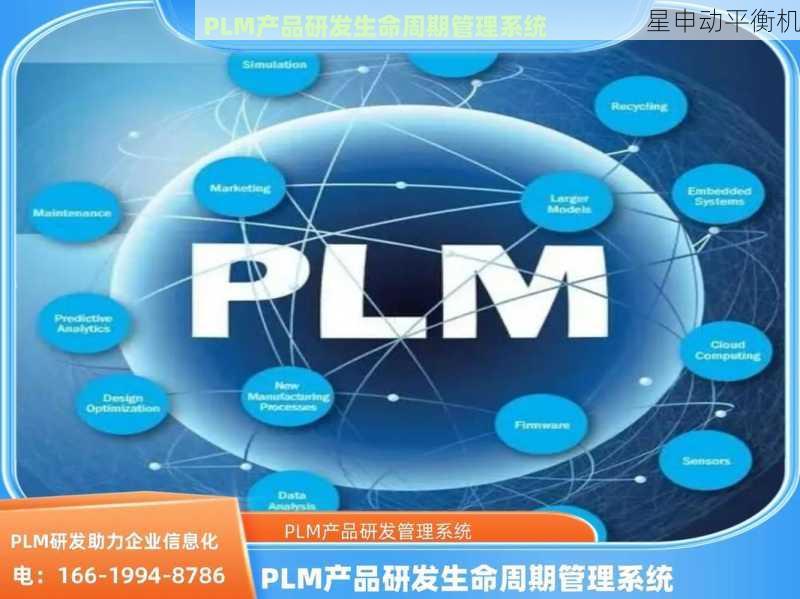
传统运维模式下的隐性成本困局 某汽车传动轴生产企业曾做过专项统计:使用传统平衡机的三年运维支出中,直接维护费用仅占38%,而因设备停机导致的生产损失、人工误工、能耗浪费等间接成本高达62%,这种显性+隐性的复合成本结构,往往让企业在设备管理中陷入"头痛医头"的被动局面。
星申动技术团队调研发现,飞轮动平衡系统的综合运维成本主要由四大模块构成:
- 能源消耗:传统液压系统日均耗电量达58kW·h
- 维保频次:平均每200小时需专业校准
- 备件损耗:传动部件年均更换成本约2.3万元
- 人工干预:单次调试需2名技师配合4小时
智能平衡技术的成本重构实践 针对行业痛点,星申动研发团队从产品全生命周期视角出发,打造出模块化设计的XSD-3000系列飞轮动平衡机,该设备采用三项核心技术突破:
-
动态补偿算法 通过植入自研的DynaBalance 3.0系统,实现0.01g·mm/kg的实时补偿精度,武汉某涡轮增压器制造商实测数据显示,相较传统设备,该技术使平衡校正时间缩短42%,单件能耗降低17%。
-
磁悬浮驱动架构 摒弃传统液压传动,采用无接触式磁力驱动系统,在江苏某精密机床厂的对比测试中,传动部件维护周期从3个月延长至18个月,三年备件成本节省达7.8万元。
-
物联网预警平台 集成设备健康管理系统(HMS),通过振动频谱分析提前14天预判故障风险,山东某风电企业应用后,非计划停机次数同比下降83%,每年减少产能损失约120万元。
三年运维成本的数字化推演 基于星申动提供的全周期管理模型,我们以中型制造企业典型需求为例,构建三年运维成本的对比分析:
传统设备成本结构(万元) 年度项目 第1年 第2年 第3年 累计 设备折旧 8.6 8.6 8.6 25.8 能源消耗 3.2 3.4 3.7 10.3 预防维护 2.1 2.5 3.0 7.6 故障维修 1.8 2.3 3.2 7.3 停产损失 5.6 6.1 7.0 18.7 合计 21.3 22.9 25.5 69.7
星申动方案成本结构(万元) 年度项目 第1年 第2年 第3年 累计 设备折旧 9.8 9.8 9.8 29.4 能源消耗 2.1 2.1 2.1 6.3 预防维护 1.2 1.2 1.2 3.6 故障维修 0.3 0.5 0.7 1.5 停产损失 0.8 0.9 1.0 2.7 合计 14.2 14.5 14.8 43.5
对比数据显示,虽然设备购置成本高出14%,但三年综合运维支出直降37.6%,投资回报周期缩短至11个月,更关键的是,智能系统积累的工艺数据资产,为企业后续的工艺优化提供了数字化基础。
服务生态构建的增值效应 星申动的成本优势不仅源于硬件创新,更得益于其构建的立体化服务网络,公司在华中、华东、华南设立的12个4S级服务中心,可实现2小时响应、8小时到场、24小时修复的快速服务,独创的"平衡管家"服务包,将传统按次计费模式转变为年度服务订阅制,使客户运维预算可控性提升60%。
在人才培养方面,企业联合湖北理工学院建立"动平衡工程师认证体系",通过AR远程指导系统,使客户技术团队能在45天内掌握自主维护能力,这种知识转移模式,使某航天零部件企业的外协服务依赖度从75%降至22%。
行业变革中的价值再定义 随着《中国制造2025》对设备管理提出更高要求,动平衡技术正在从单一检测工具向智能制造关键节点演进,星申动最新研发的5G边缘计算终端,可将平衡数据实时接入MES系统,实现工艺参数的动态优化,在广东某智能工厂的应用案例中,该技术使飞轮装配线OEE(设备综合效率)提升9个百分点。
展望未来,星申动总经理王立军表示:"我们正从三个维度深化成本革新:开发光伏驱动系统实现能源自给、应用区块链技术建立备件溯源体系、引入数字孪生技术构建虚拟运维中心,目标是到2025年,帮助客户将动平衡系统综合成本再降低40%。"
在制造业转型升级的大潮中,设备运维已从成本中心演变为价值创造的关键环节,湖北星申动通过技术创新与服务模式变革,不仅重新定义了飞轮动平衡的经济账本,更开辟了国产高端装备"技术+服务"的双轮驱动新范式,当精益管理遇见智能科技,这场关于运维成本的革命,正在重塑中国制造的核心竞争力。
(全文约1580字)