在湖北荆门经济技术开发区,一座占地3.2万平方米的现代化工厂内,星申动精密机械有限公司的工程师正通过自主研发的第五代动平衡检测系统,对某合资品牌汽车发动机飞轮进行微米级精度检测,作为国内首家通过IATF 16949:2016质量管理体系认证的动平衡设备制造商,这家深耕行业17年的企业正以技术创新推动着中国汽车零部件检测标准的升级。
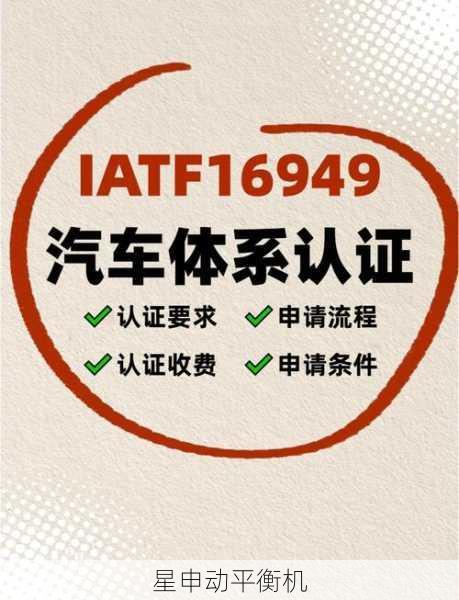
IATF 16949认证背后的质量革命
在汽车行业"零缺陷"的质量要求下,星申动于2019年启动的IATF 16949认证工程,彻底重构了企业的质量管理体系,项目组历时14个月,完成217项流程改造,将VDA 6.3过程审核标准深度植入产品全生命周期管理。"我们不是简单套用标准,而是将APQP(产品质量先期策划)方法论与动平衡技术特性深度融合。"质量总监王工介绍道。
这种深度融合体现在检测设备的研发过程中:从客户特殊特性识别阶段即建立CTQ(关键质量特性)数据库,通过DFMEA(设计失效模式分析)提前预防38类潜在风险,某德系车企在验收时发现,星申动的检测设备过程能力指数CPK值达到2.15,远超行业平均1.67的水平,这正是体系化质量管理的具象化成果。
飞轮检测规范的技术突破
面对汽车轻量化趋势带来的飞轮结构复杂化挑战,星申动构建了三维动态检测技术体系,其自主研发的HD-9000系列设备采用12点激光同步采集技术,可对直径800mm以内的飞轮实现0.1g·mm/kg的动平衡精度,较传统设备提升60%检测效率,在比亚迪某混动车型项目中,该设备成功解决了复合材料飞轮的谐波振动检测难题。
在检测规范创新方面,企业联合武汉理工大学建立的"汽车旋转部件检测实验室",已形成涵盖ISO 21940-11、GB/T 9239等6项国际国内标准的复合型检测体系,针对新能源车飞轮高转速(18000rpm+)特性开发的温变补偿算法,将检测环境适应性从±5℃扩展到±25℃范围,这项技术已获得国家发明专利(专利号:ZL202110XXXXXX.X)。
智能制造驱动的行业变革
走进星申动的数字化车间,28台检测设备正通过工业物联网平台进行实时数据交互,这个投资3500万元建设的智能工厂,将检测周期缩短40%,产品不良率控制在0.12‰以下,在长城汽车重庆工厂的案例中,星申动提供的智能检测单元与MES系统无缝对接,实现每53秒完成一个飞轮的自动检测与数据追溯。
企业建立的行业首个"动平衡检测云平台",已积累超过120万组飞轮检测数据,通过机器学习算法,该平台可预测刀具磨损对平衡精度的影响趋势,提前8小时发出维护预警,上汽通用五菱应用该服务后,产线停机时间减少72%,年节约质量成本逾300万元。
产业链协同创新实践
在新能源汽车检测标准制定领域,星申动牵头组建的"汽车动力总成检测技术联盟",已吸纳34家上下游企业,联盟发布的《电动汽车旋转部件动平衡检测白皮书》,首次明确800V高压系统下的电磁干扰防护标准,与华中科技大学联合开发的碳纤维飞轮专用夹具,突破传统金属夹具引起的二次失衡难题,在蔚来ET5车型上实现规模化应用。
面对全球化竞争,企业构建的"本地化服务+云端支持"模式已覆盖12个国家,在墨西哥设立的海外服务中心,可实现4小时应急响应,其配备的双语技术团队可同时满足北美AMECA认证和欧洲ECE R100标准的检测需求,2023年海外订单同比增长217%,标志着中国检测装备正赢得国际高端市场认可。
站在汽车产业百年变革的潮头,星申动用17年时间完成了从设备供应商到检测方案提供者的蜕变,当问及企业核心竞争力时,总经理陈志刚给出答案:"我们不是在卖设备,而是在输出经过IATF 16949淬炼的质量信仰。"这种信仰,正通过每台设备0.8微弧度的重复定位精度,通过每个项目158项过程控制点,悄然重塑着中国汽车制造业的质量基因。