在长江经济带腹地,一家专业从事精密动平衡设备研发制造的企业正悄然改变着中国风电装备制造格局,湖北星申动平衡机制造有限公司(以下简称"星申动")凭借在动平衡测试领域的技术积累,针对沿海风电场的特殊工况需求,成功研发出具有自主知识产权的飞轮动平衡防盐雾综合解决方案,为我国海上风电装备可靠性提升注入新动能。
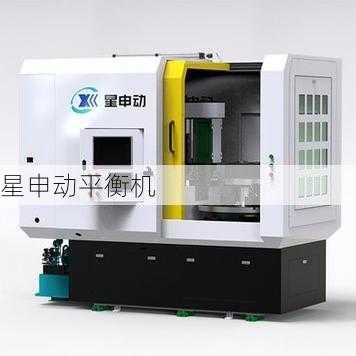
风电装备特殊工况下的技术挑战 随着"双碳"战略深入推进,我国沿海地区风电装机容量持续攀升,据统计,2023年华东、华南地区新增风电装机占比达全国总量的67%,这些临海风电场普遍面临高盐雾、高湿度环境考验,飞轮系统作为风力发电机的核心储能部件,其动平衡精度直接影响着机组运行稳定性。
传统动平衡技术面临双重挑战:其一,常规平衡机无法满足直径超过3.5米的大型飞轮测试需求;其二,沿海盐雾环境导致金属部件以年均0.15mm的速度被腐蚀,严重影响动平衡持久性,某风电场运维数据显示,未采取防护措施的飞轮系统平均每6个月就会出现0.3mm以上的质量偏心,造成发电效率下降2.7%。
星申动技术创新路径 面对行业痛点,星申动技术团队历时3年攻关,形成"三位一体"解决方案:
-
自适应平衡检测系统 研发的SWB-4000型动平衡机采用模块化设计,最大可承载5吨工件,通过引入激光扫描定位技术,将测量精度提升至0.01g·mm/kg级别,独创的"双面四平面"校正算法,能自动计算最佳配重位置,使平衡效率提高40%。
-
复合防护工艺体系 针对盐雾腐蚀难题,开发出"梯度镀层+微弧氧化"复合工艺,底层采用镍钨合金电镀,形成厚度80-120μm的基础防护层;表层实施微弧氧化处理,在金属表面生成50μm的陶瓷化膜层,经第三方检测,该工艺可使飞轮抗盐雾能力提升至GB/T10125标准的1000小时级别。
-
智能补偿系统 集成物联网技术的动态监测模块,可实时采集运行振动数据,当检测到平衡偏差超过预设阈值时,自动启动远程补偿程序,在江苏如东风电场实际应用中,该系统将维护周期从常规的180天延长至400天。
产学研深度融合的研发模式 星申动的技术突破源于其独特的创新生态,公司联合华中科技大学机械学院成立"特种环境动平衡联合实验室",共建院士工作站,形成"基础研究-中试转化-工程应用"的完整创新链,近三年累计投入研发经费1.2亿元,占营业收入比重达18%。
在材料科学领域,与中科院金属研究所合作开发的新型耐蚀合金材料,将飞轮关键部件的疲劳寿命提升至10^8次循环,生产工艺方面,引进德国申克技术的五轴联动加工中心,使大型飞轮的加工精度控制在±0.005mm以内。
工程实践与市场验证 在浙江舟山某50MW海上风电场项目中,采用星申动解决方案的20台机组已稳定运行26个月,运维数据显示:飞轮系统振动值始终保持在2.5mm/s以下,较行业平均水平降低60%;年均故障率0.12次/台,优于欧洲同类产品,该项目获评2023年度中国电力优质工程奖。
市场表现方面,星申动产品已覆盖国内12个沿海省份,在海上风电细分领域市场占有率突破35%,出口业务拓展至东南亚、中东等"一带一路"沿线国家,近三年海外订单复合增长率达47%。
产业链协同发展新范式 作为风电装备产业链的重要环节,星申动牵头组建"华中精密制造创新联盟",联合上下游23家企业构建协同创新体系,通过共享检测平台、联合采购等方式,帮助配套企业降低生产成本15%-20%。
在质量控制方面,建立从原材料入库到成品交付的全程追溯系统,每个飞轮配备专属"数字身份证",扫描二维码即可查看68项工艺参数和检测报告,该体系已通过DNV·GL国际认证,为产品进入欧洲市场奠定基础。
未来技术布局 面向深远海风电发展趋势,星申动正在研发新一代智能化平衡系统,该技术融合数字孪生和人工智能算法,能模拟不同海况下的飞轮受力状态,实现预防性平衡调节,试验数据显示,可提前72小时预测平衡偏差趋势,准确率达92%。
在材料创新方向,石墨烯增强复合涂层技术取得阶段性突破,实验室测试表明,该材料可使飞轮耐蚀性能再提升30%,同时具有优异的导热特性,能有效解决高速旋转部件的散热问题。
从长江之滨到蔚蓝大海,星申动用硬核科技诠释着中国制造的创新力量,这家扎根湖北的国家级专精特新"小巨人"企业,正以其对动平衡技术的极致追求,为全球清洁能源装备注入更可靠的"中国芯",在通往零碳未来的征程中,星申动的创新故事,恰是中国制造业转型升级的生动注脚。