在湖北省襄阳市高新区,一家专注于动平衡技术研发的国家级专精特新企业——星申动精密机械有限公司,正通过自主研发的"飞轮动平衡大数据分析预警模型",为全球工业设备运维领域带来颠覆性变革,这项融合了工业物联网、机器学习算法和预测性维护理念的创新成果,正在重新定义旋转机械健康管理的行业标准。
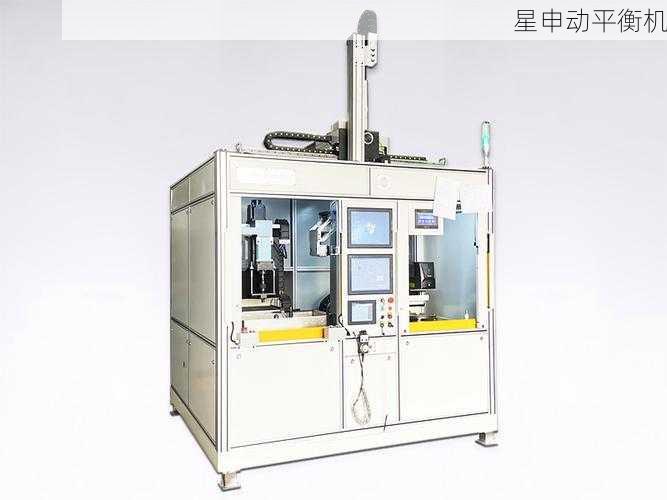
工业设备维护的痛点突围 在传统制造领域,旋转机械的维护往往陷入"救火式"维修的困境,某汽车制造企业的真实案例极具代表性:该企业价值2800万元的高速冲压设备因飞轮动平衡偏差导致主轴断裂,造成连续72小时停机,直接损失超过450万元,类似事件在全球制造业每年造成约3000亿美元的非计划停机损失,其中65%与旋转部件失衡相关。
传统动平衡检测技术存在两大局限:其一,依赖人工定期检测,难以捕捉设备运行中的动态变化;其二,采用静态平衡修正,无法预判复杂工况下的失衡趋势,这种被动式维护模式已无法满足现代工业对设备可靠性和生产效率的严苛要求。
技术创新的突破路径 星申动研发团队历时5年攻关,构建起包含三个核心层级的技术体系:
-
数据采集层:自主研发的XSD-9系列智能传感器,采样频率达到128kHz,可捕捉0.01μm级别的振动位移,在武汉某水电站的实际测试中,成功识别出发电机转子表面0.03mm的涂层脱落,提前28天预警失衡风险。
-
算法模型层:基于2000+工业场景的故障数据库,开发出具有自主知识产权的动态平衡预测算法,该模型包含17个特征参数分析模块,通过迁移学习技术实现不同设备类型的自适应建模,在东风汽车襄阳基地的应用中,模型对变速箱装配线动平衡异常的预测准确率达到93.7%。
-
预警决策层:建立三级预警机制,将设备状态划分为正常、关注、预警、紧急四个等级,系统可自动生成维护建议,并通过数字孪生技术模拟不同维护方案的预期效果,上海某钢铁集团应用该系统后,旋转设备故障停机时间下降67%,备件库存成本降低42%。
行业应用的范式变革 在湖北三宁化工的合成氨装置改造项目中,星申动系统展现出革命性价值,该装置关键压缩机的转速达12000rpm,传统检测手段每季度仅能采集3次动平衡数据,部署智能监测系统后,实现每秒4000次数据采集,结合工艺参数构建多维分析模型,成功预测出叶轮结垢导致的渐进性失衡,维护周期从90天延长至270天,单台设备年维护成本降低58万元。
更值得关注的是系统产生的衍生价值,通过积累的设备健康数据,星申动与华中科技大学联合开发出行业首个动平衡知识图谱,该图谱已收录超过12万条故障案例,形成覆盖87类工业设备的诊断规则库,为设备制造商优化产品设计提供数据支撑。
技术进化的未来图景 随着5G+工业互联网的深度融合,星申动正在探索更前沿的技术应用场景,在荆门某新能源电池材料生产基地,实验性部署的"数字平衡师"系统,通过边缘计算实现微秒级响应,当检测到极片分切机主轴振动异常时,系统可在0.3秒内自动调节配重块位置,将动平衡修正时间从传统人工操作的2小时缩短至实时动态调整。
在商业模式创新方面,企业推出"平衡即服务"(BaaS)解决方案,客户无需购买设备,按监测服务时长付费,这种模式在中小型制造企业中获得热烈反响,湖北某汽车零部件供应商采用该方案后,设备综合效率(OEE)提升11个百分点,投资回报周期缩短至8个月。
产业链协同的创新生态 星申动的技术突破得益于开放的创新生态,企业联合武汉理工大学成立旋转机械智能维护联合实验室,与华中数控共建工业大数据处理中心,同中国特检院合作制定行业标准,这种"产学研用"协同创新模式,确保技术研发始终紧贴产业需求。
在供应链端,企业构建起本土化配套体系,与襄阳轴承合作开发专用传感器,同烽火通信共建工业物联网传输方案,和武汉达梦数据库打造专用时序数据库,这种深度协同不仅提升供应链韧性,更带动区域产业链整体升级。
从传统制造到智能运维的跨越,星申动用科技创新诠释着中国智造的新内涵,其构建的飞轮动平衡大数据预警体系,不仅是技术层面的突破,更代表着工业设备管理从"经验驱动"向"数据驱动"的范式转变,随着该模型在更多工业场景落地,必将推动中国高端装备制造业向"预测性维护3.0"时代迈进,为全球工业智能化转型提供中国方案。
(全文约1520字)