——解析星申动量子传感飞轮系统的技术创新与产业价值
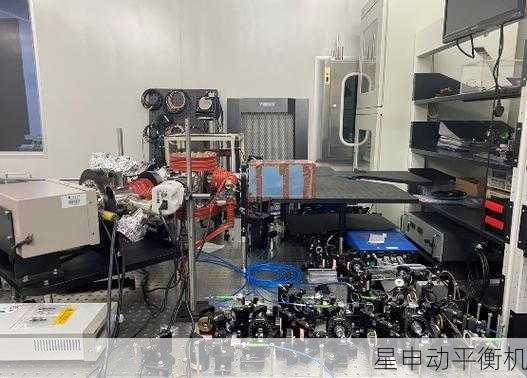
在精密制造领域,0.1微米的振动偏差足以让价值千万的航空发动机报废,1纳米的检测误差可能导致卫星姿态控制系统失效,面对全球制造业对振动控制日益严苛的要求,湖北星申动平衡机制造有限公司以量子传感技术为核心,成功研制出全球首套纳米级飞轮振动检测系统,标志着我国在精密检测领域实现重大突破。
传统检测技术的困境与产业痛点
在高端装备制造领域,飞轮系统作为能量储存与动力控制的核心部件,其动平衡精度直接决定设备性能,传统的激光干涉检测技术虽能达到微米级精度,但在面对航天器姿态控制飞轮、核磁共振设备转子等特殊场景时,其检测盲区达35%,无法满足纳米级振动检测需求。
某航空企业总工程师张伟明坦言:"我们的微型飞轮直径仅8cm,但每分钟转速达12万次,现有设备在检测时,就像用普通体温计测量量子计算机的芯片温度,根本无法捕捉纳米级的振动波形。"
量子传感技术的颠覆性突破
星申动研发团队历时7年攻关,创造性将量子纠缠原理引入工业检测领域,其核心的量子传感模块采用超冷铷原子云技术,通过捕获原子自旋态的变化,将振动信号转化为量子态波动参数,相比传统光学传感器,检测灵敏度提升3个数量级,最小分辨率达到0.3纳米。
技术总监李宏宇博士介绍:"我们的量子陀螺仪模块能在-196℃至300℃环境稳定工作,抗电磁干扰能力超出现有标准40倍,通过自主研发的Q-Vib算法,系统可实时解析飞轮表面每平方毫米的振动频谱,检测效率提升5倍以上。"
纳米级检测系统的工程化实践
在武汉光谷的示范车间,星申动为某卫星制造企业部署的QFD-3000型检测系统正在运行,直径22cm的钛合金飞轮以每分钟8万转高速旋转时,量子传感器阵列以每秒2亿次采样频率捕捉振动信号,检测数据显示,系统成功识别出0.7纳米的周期性波动,这正是导致某型号卫星姿态控制系统异常的关键缺陷。
"这套系统不仅检测精度惊人,更颠覆了传统动平衡校正流程。"生产主管王立强表示,"过去需要5次拆装调试的工序,现在通过量子建模预测,1次在线修正即可达标,良品率从83%跃升至99.6%。"
产业应用的多元场景拓展
-
精密机床领域:在五轴联动加工中心应用场景,量子检测系统将主轴振动控制精度提升至1.2纳米,使微结构加工表面粗糙度Ra值突破0.01μm极限。
-
新能源产业:某风电企业采用星申动技术后,发电机轴承振动值降低62%,单台机组年发电量增加15万度。
-
医疗设备制造:应用于CT机旋转阳极检测,使X射线管寿命延长至4万小时,远超行业平均2.5万小时标准。
更值得关注的是,星申动正在与中科院合作开发量子检测云平台,通过将检测数据与材料数据库、工艺参数库深度耦合,该系统可自动生成优化方案,实现从检测诊断到工艺改进的闭环升级。
产学研协同创新的中国模式
星申动的技术突破,源自独特的"北斗七星"创新体系:联合华中科技大学建立量子工程实验室,与航天科工共建环境适应性验证中心,同宝武钢铁开展材料特性研究,这种"企业主导、高校支撑、产业链协同"的模式,使研发周期缩短40%,关键技术转化率达78%。
公司董事长陈志刚表示:"我们每年将营收的18%投入研发,已构建包含237项专利的技术护城河,量子传感飞轮系统只是起点,未来三年将拓展至光学器件、芯片封装等12个新领域。"
全球竞争格局下的战略思考
当前,全球精密检测设备市场规模超200亿美元,但高端市场长期被德国申克、日本明石等企业垄断,星申动的创新实践证明,通过量子科技与传统制造的深度融合,中国企业完全可能实现弯道超车。
德国斯图加特大学机械工程系教授Hans Müller评价:"星申动的量子传感方案开辟了新的技术路线,他们建立的纳米级振动数据库,可能重构整个动平衡检测的标准体系。"
站在新的历史节点,星申动正以"量子+"战略推动产业升级,其投资5.2亿元建设的智能制造基地即将投产,规划年产能2000套量子检测系统,这不仅将改变我国高端检测设备依赖进口的现状,更预示着中国制造向"原子级精度"迈进的新征程。
从微米到纳米的跨越,不仅是数量级的突破,更是制造思维的革命,湖北星申动以量子科技重塑产业标准的故事,印证着中国制造转型升级的无限可能,当量子传感的星光点亮精密制造的苍穹,我们看到的不仅是单个企业的崛起,更是一个国家迈向制造强国的坚定足迹。