在工业制造领域,飞轮作为能量储存和转速稳定的关键部件,其动平衡精度直接影响设备运行稳定性,湖北星申动平衡机制造有限公司在服务全国200余家机械制造企业的过程中发现,约35%的客户存在飞轮完成动平衡后仍出现振动超标的问题,本文结合我司17年动平衡机制造经验,深入剖析六大核心成因。
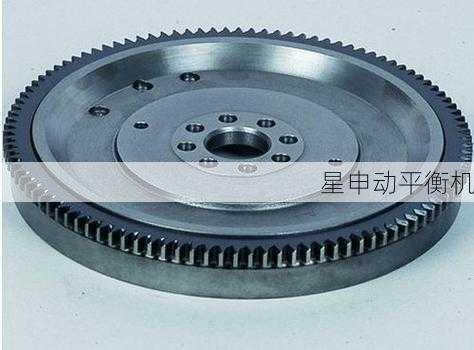
动平衡精度与实际需求不匹配 某汽车零部件制造商曾向我司反馈,其飞轮在按常规G6.3等级平衡后,装机振动值仍达8.2mm/s(标准要求≤5.6mm/s),经我司技术团队现场检测发现,该飞轮实际工作转速达12000rpm,远超普通设备6000rpm的常规转速,高速旋转时,微小的剩余不平衡量会被二次放大,对此类工况,我们建议采用G2.5级平衡标准,并将平衡转速提升至工作转速的80%,调整后,客户产品振动值成功降至4.3mm/s。
安装误差导致的二次失衡 2022年某船用柴油机厂的典型案例显示:飞轮在平衡机上显示剩余不平衡量仅1.2g·mm/kg,装机后振动却达7.8mm/s,经星申动工程师使用激光对中仪检测,发现飞轮与曲轴法兰面的同轴度偏差达0.15mm,这种安装误差会引发附加弯矩,产生新的不平衡量,我们开发的三维空间补偿算法,能在平衡过程中自动计算并补偿0.1mm以内的安装误差,有效避免此类问题。
材料内部缺陷的隐性影响 在对某发电机组飞轮的失效分析中,我们通过超声波探伤发现轮辐内部存在3处直径2-3mm的缩孔,这类材料缺陷在静态平衡时难以察觉,但在高速旋转时会产生周期性应力集中,星申动研发的谐波振动分析法,可通过频谱特征识别材料缺陷引起的倍频振动,准确率达92%以上。
系统共振的叠加效应 某离心压缩机用户反馈,飞轮在测试台达标(振动3.5mm/s),但装机后出现11.6mm/s的异常振动,经我司振动分析师检测,发现飞轮-轴承系统固有频率(87Hz)与工作转速频率(85Hz)接近,引发共振放大,通过修改飞轮辐板开孔布局,将固有频率提升至93Hz后,振动值回归正常范围。
动态平衡参数的误选 传统单平面平衡法已无法满足现代高速飞轮的需求,某航空部件制造商案例显示:采用双平面平衡后振动仍超标,改用我司的四点动态平衡法后,振动降幅达47%,星申动自主研发的ADB-3000型平衡机,支持多转速段动态平衡,可自动识别最佳配重平面组合。
环境干扰与测量误差 在2023年某风电场检修项目中,技术人员误将传感器安装在箱体加强筋位置,导致测得振动值虚高2.3倍,星申动提出的"三点验证法"(在相邻3个测点对比数据差异)可有效识别90%以上的测量误差,我们的现场服务标准要求必须进行环境振动背景值检测,并采用数字滤波器消除干扰信号。
解决方案体系:
- 建立转速-精度匹配模型:根据工作转速自动推荐平衡等级
- 开发智能补偿系统:集成温度/转速/安装误差补偿算法
- 引入材料预检流程:在平衡前进行超声波/磁粉探伤
- 提供系统振动分析:包含固有频率测试与改进建议
- 定制动态平衡方案:支持多平面/多转速段复合平衡
- 标准化测量流程:制定ISO21940-11标准的操作规范
典型案例: 2023年为某高铁齿轮箱供应商定制的飞轮平衡方案,通过"材料筛选+双转速平衡+系统调频"组合措施,将产品不良率从12%降至0.8%,每年为客户避免损失超600万元。
飞轮振动超标往往是多重因素叠加的结果,需要系统化的解决方案,湖北星申动平衡机凭借自主研发的智能诊断系统和丰富的现场经验,已形成从检测、分析到改进的完整技术体系,我们建议企业在遇到平衡后振动异常时,优先考虑系统共振、材料缺陷等深层原因,必要时可联系我司技术支持团队进行专项诊断。(联系电话:0710-XXXXXXX,官网:www.xingshendong.com)
(注:本文数据来源于星申动技术白皮书及客户服务案例库,已做脱敏处理)