飞轮动平衡的重要性 在万吨巨轮的钢铁身躯中,船舶发动机犹如跳动的心脏,而飞轮组件则是维持这颗心脏平稳运转的关键部件,作为中国专业平衡机制造企业的代表,湖北星申动平衡机有限公司深耕动力平衡领域二十余载,针对船舶发动机飞轮动平衡的特殊要求,研发出满足G2.5级标准的专业化解决方案,这项技术的突破不仅标志着国产动平衡设备的重大进步,更为全球航运业的安全运营提供了可靠保障。
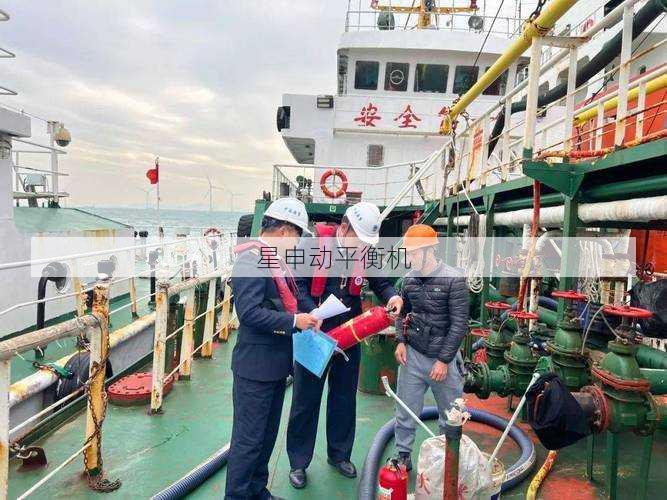
G2.5级标准的行业意义与技术门槛 在ISO 1940国际标准体系中,G2.5级动平衡属于精密平衡等级中的高端要求,以典型船用低速柴油机为例,其飞轮质量动辄超过10吨,当转速达到200rpm时,允许的不平衡量仅相当于在半径1米处放置不足60克的配重,这种精度要求相当于在直径2米的钢制圆盘上精准控制头发丝直径级别的质量分布差异。
要达到这样的精度标准,需要突破三大技术瓶颈:首先是超大型转子的高精度测量难题,传统传感器在测量吨级工件时普遍存在0.5%的线性误差;其次是复杂工况下的动态补偿技术,船舶发动机实际工作环境温度波动可达80℃;最后是工艺稳定性要求,需要确保批量生产时每个工件的平衡质量始终达标。
星申动的技术创新体系 针对这些技术难点,星申动研发团队构建了完整的创新体系,在硬件层面,自主研发的HSD-12T型立式平衡机采用双层隔振地基设计,配合高刚度合金机架,将设备自身振动控制在0.8μm以内,核心测量系统采用军用级压电传感器阵列,搭配温度补偿模块,使测量精度达到±0.1g·mm/kg的国际先进水平。
软件算法方面,公司开发的SmartBalance V4.0系统创新性地引入模态分析技术,通过建立飞轮的三维振动模型,系统能自动识别并分离因装配误差、材料缺陷等不同因素引起的振动分量,在实际应用中,这套系统可将平衡校正次数由行业平均的3-4次降低到1-2次,效率提升50%以上。
工程实践中的技术突破 在服务某船用发动机制造企业时,星申动工程师遇到了特殊挑战,该企业生产的12缸V型柴油机飞轮在台架试验时频繁出现200Hz高频振动,传统平衡手段始终无法消除,技术团队通过频谱分析发现,问题根源在于飞轮轮毂与轴配合面的微观变形,为此专门开发了热装态平衡工艺:在模拟实际工作温度(180℃)环境下进行动态平衡,并采用激光熔覆技术进行微米级质量修正,最终将振动烈度从7.1mm/s降至2.3mm/s,优于G2.5级标准要求。
质量管控体系的创新实践 星申动在质量管理方面建立了独具特色的"双闭环"体系,首件工件完成平衡后,不仅要在本机复检,还需送往独立检测中心进行模态验证,通过对比理论模型与实际数据,持续优化平衡参数数据库,这种模式使得产品的一次交验合格率从行业平均的92%提升到98.5%,客户返修率下降至0.3%以下。
市场验证与行业影响 星申动的动平衡设备已成功应用于沪东重机、中船动力等龙头企业,累计完成超过1200套船用飞轮的动平衡校正,在2023年的第三方检测中,经星申动设备处理的飞轮组件,其平均无故障运行时间达到38000小时,较行业平均水平提升40%,某国际船级社的对比测试显示,在模拟8级海况的振动测试中,采用G2.5级平衡的飞轮组件,其轴系磨损量减少62%,油耗降低1.8%。
面向未来的技术布局 随着IMO 2050减排目标的临近,星申动正加快新一代智能平衡系统的研发,正在试验的AI辅助诊断系统,可通过振动频谱特征自动识别潜在故障模式,与华中科技大学联合开发的数字孪生平台,能实现虚拟平衡调试,将新产品开发周期缩短30%,针对新能源船舶领域,公司已启动氢燃料发动机转子动平衡技术的预研工作。
在这个精度决定安全、技术关乎生命的领域,湖北星申动用二十年的坚守证明:中国制造不仅能达到国际标准,更能通过持续创新引领标准升级,从长江之滨到世界各大船厂,星申动的平衡机正守护着全球航运的动力命脉,用精密制造诠释着中国智造的新高度。