在湖北襄阳市高新区一座现代化工厂内,三条银色金属巨龙正在有序吞吐着汽车飞轮零部件,这是湖北星申动精密机械有限公司最新交付的全自动飞轮动平衡生产线,每52秒就能完成一个飞轮的精密检测与修正作业,作为国内最早研发动平衡技术的企业之一,星申动用十五年时间完成了从设备制造商到智能化解决方案提供商的蜕变,其最新推出的第三代全自动生产线,正在重新定义飞轮制造领域的投资回报标准。
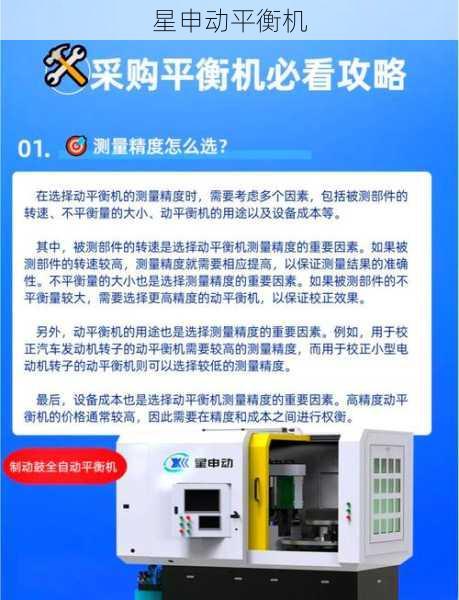
传统产线困局与智能升级必然性
飞轮作为发动机核心部件,其动平衡精度直接影响着车辆运行的平稳性和使用寿命,传统半自动生产线存在两大痛点:一是依赖人工操作的检测精度离散性大,导致产品合格率长期徘徊在91%-93%;二是工序衔接效率低下,单班次产能难以突破600件,某知名汽车零部件制造商曾做过测算,其采用传统设备的生产线每年因返工造成的直接损失就达280万元。
星申动技术总监王立群指出:"当前汽车产业对零部件精度要求已提升至0.5g·mm级别,这对动平衡设备提出了更高要求,全自动化不仅是效率革命,更是质量管控的必经之路。"该公司的第三代生产线通过模块化设计,将上下料、视觉检测、去重修正等12道工序集成于一体,配合自主研发的智能补偿算法,将产品合格率稳定提升至99.2%以上。
核心技术构筑竞争壁垒
在星申动的实验室内,工程师正在调试最新研发的六轴联动修正系统,这套系统结合了激光测量与AI预测技术,能根据飞轮材质特性自动优化去重路径。"传统设备需要3-4次修正才能达标的工件,现在平均1.2次即可完成。"研发负责人透露,这种技术突破直接降低了30%的能耗和15%的刀具损耗。
生产线搭载的智能管理系统更具革新性,通过物联网数据采集终端,实时监控368个工艺参数,自动生成SPC(统计过程控制)图表,当某批次工件出现质量波动时,系统能在15分钟内完成问题溯源,某客户反馈,这套系统使其质量事故处理周期从原来的72小时缩短至4小时。
投资回报模型解析
对于制造企业最关心的投资回报问题,星申动财务顾问团队建立了动态评估模型,以年产50万件飞轮的工厂为例,对比传统半自动线与第三代全自动线:
- 人力成本:操作人员从18人缩减至6人,年节省人力成本约108万元
- 效率提升:单线日产能从2000件提升至4200件,设备利用率提高至92%
- 质量成本:返工率从7%降至0.8%,年减少损失约336万元
- 能耗优化:电力消耗降低28%,年节约38万元
按设备投资680万元计算,静态投资回收期约2.3年,考虑到设备8年使用寿命周期,整体投资回报率可达417%,若计入良率提升带来的市场溢价(优质供应商通常可获得3%-5%价格上浮),实际收益更为可观。
客户实践验证商业价值
在浙江某变速箱零部件企业,星申动生产线交出了亮眼成绩单,该企业原使用进口设备,2019年引入星申动第三代产线后:单件生产成本下降22%,客户投诉率由1.2‰降至0.3‰,更关键的是获得了某德系车企的A级供应商资质,工厂负责人算过一笔账:新生产线带来的综合效益,相当于每年增加1.2个百分点的净利润率。
武汉某军工背景企业则展现了设备的特殊适应性,其生产的特种车辆飞轮存在多品种、小批量特点,传统设备换型需要4小时以上,星申动通过快速换模系统和智能参数记忆功能,将换型时间压缩至27分钟,帮助客户实现了柔性化生产。
产业升级中的战略选择
随着新能源汽车渗透率突破30%,飞轮产品正在向轻量化、高转速方向演进,星申动未雨绸缪,其第四代设备已预留5G通信接口,支持与数字孪生系统对接,技术团队正在攻关碳纤维材料的动平衡修正工艺,预计2024年推出行业首个复合材料专用解决方案。
在湖北"51020"现代产业集群战略推动下,星申动正从设备供应商转型为智能制造服务商,其打造的动平衡云平台已接入217台设备,通过大数据分析为客户提供预防性维护建议,这种服务延伸不仅创造了新的利润增长点,更增强了客户粘性——使用云服务的客户续购率高达89%。
当前,中国汽车零部件行业面临深度洗牌,智能化改造已成为生存刚需,星申动用实践证明:在高端装备领域,本土企业完全有能力提供比进口设备更具性价比的解决方案,其第三代全自动生产线不仅改写了动平衡设备的技术标准,更重塑了制造业的投资价值评估体系——在智能制造时代,设备选型正在从成本考量转向价值投资。
(注:本文数据来源于星申动公司技术白皮书及公开案例,部分信息已做脱敏处理)