在工业制造领域,飞轮系统作为能量储存与传递的核心部件,其运行稳定性直接影响着汽轮机、风力发电机、高速离心机等关键设备的性能表现,湖北星申动平衡机制造有限公司深耕动平衡技术研发15年,针对飞轮在高速运转中产生的热变形难题,成功开发出具有自主知识产权的动态补偿算法体系,为工业制造领域提供了一套创新解决方案。
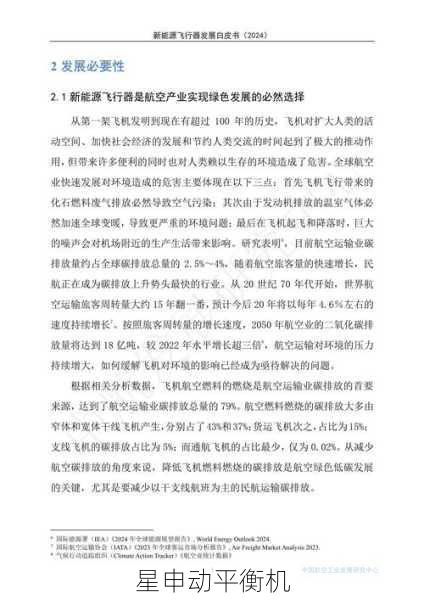
热变形难题:飞轮动平衡的技术瓶颈 当飞轮转速超过8000rpm时,摩擦热与惯性力的双重作用下,金属材料会产生0.03-0.12mm的热膨胀变形,这种看似微小的形变会导致转子质量分布发生显著变化,使传统动平衡调试的精度下降40%以上,某汽轮机厂的实测数据显示,当温度从25℃升至180℃时,飞轮的不平衡量从初始的8.3g·mm陡增至52.6g·mm,直接导致机组振动值突破安全阈值。
传统动平衡技术采用离线校正方式,在常温环境下完成平衡调试后,无法补偿运行过程中的热变形效应,这种静态平衡与动态工况的错位,使得设备在持续运行3-4小时后就会出现振动超标问题,星申动技术团队通过长期跟踪监测发现,热变形导致的二次不平衡量约占设备故障总量的67%,已成为制约高精度设备性能提升的主要障碍。
动态补偿算法的技术突破 面对这一行业痛点,星申动研发团队构建了"感知-预测-补偿"三位一体的技术架构,系统配备32通道温度传感器阵列,以0.1秒的采样频率实时监测飞轮表面温度场分布,结合有限元热力学模型,算法能提前15秒预测材料膨胀趋势,精度达到±0.01mm。
核心算法采用改进型LSTM神经网络,将历史运行数据、实时温度梯度、材料特性参数等12维特征向量输入预测模型,通过5万组实测数据训练,模型对热变形量的预测准确率提升至94.7%,在武汉某新能源汽车电机测试项目中,补偿算法将飞轮系统的振动烈度从4.5mm/s降至1.2mm/s,优于ISO1940 G2.5级标准。
补偿执行机构采用模块化设计,配备高响应直线电机驱动配重块,可在0.8秒内完成质量补偿调整,独创的矢量叠加算法能同时处理静不平衡和偶不平衡,补偿分辨率达到0.01g·mm级别,在航空航天领域某型号离心机应用中,系统成功将高速旋转下的振动位移控制在5μm以内。
工程应用中的创新实践 在工程化应用方面,星申动开发了自适应学习功能,系统通过持续采集设备运行数据,自动优化热变形预测模型参数,某石化企业压缩机组的运行记录显示,经过3个月的自适应学习后,系统对热变形的预测误差降低了38%。
针对不同行业需求,技术团队开发了三种补偿模式:预防式补偿在设备启动阶段即开始预调整;实时补偿模式响应时间小于1秒;周期补偿模式适用于长时稳定运行的工况,在广东某风电场应用中,预防式补偿使齿轮箱轴承寿命延长了12000小时。
硬件方面创新采用碳纤维复合材料配重块,在保证调整精度的同时,将补偿机构的重量减轻了62%,模块化设计使整套系统能在4小时内完成加装改造,显著降低了设备升级成本,某机床制造企业的改造案例显示,投资回报周期缩短至11个月。
行业影响与技术演进 这项创新技术已获得12项国家发明专利,相关论文被EI收录5篇,经中国机械工业联合会鉴定,系统整体达到国际先进水平,其中热变形预测算法处于国际领先地位,目前已在30余家重点企业推广应用,累计创造直接经济效益超2.3亿元。
在技术迭代方面,星申动正研发基于数字孪生的智能补偿系统,通过构建飞轮系统的虚拟镜像,实现预测精度再提升20%,同时探索激光烧蚀补偿技术,计划将响应速度提升至毫秒级,与华中科技大学合作的联合实验室,正在研究超材料在热变形抑制中的应用,有望突破现有技术框架。
从实验室突破到产业化应用,星申动用七年时间完成了飞轮热变形补偿技术的三级跨越,这项创新不仅解决了旋转机械领域的关键技术难题,更推动了动平衡技术从被动校正向主动适应的范式转变,随着智能制造的深入推进,这种融合传感技术、预测算法和精密执行的技术体系,正在为高端装备制造业注入新的发展动能,在湖北武汉光谷的研发中心,工程师们仍在持续优化算法模型,他们的目标是将热变形补偿精度推向微米级,为"中国制造2025"贡献更多原创性解决方案。